Since my last post I have done a little more reading, which has been most interesting, but not substantially changed by conclusion.
Biringuccio says about Antimony:
“The practical philosophers make great use of it in their alchemistic works, in order, they say, to make an oil that they believe gives the colour of gold to fixed silver. For this reason many of them hold it in high repute, especially the kind that has long thin fibres like a bundle of bristles. And they say that they can obtain greater results with it than Sulphur, since it is nearer the metallic species than sulphur is. This I know for certain because I have seen them extract from it a bloody liquor in the form of an oil. The alchemist who made that which I saw told me that it had not only the property of giving a golden colour to silver but also the properly of fixing silver. This may be true, but as I said, I have seen only the liquor, and I have never seen silver coloured by it or anything else.”
He also mentions that it was mined and used in Pewter and bells. Interestingly enough, one article in the journal of the Historical Mettallurgy Society says that many Bronze cooking vessels in the medieval period had around 5% Antimony, but that it was most likely from the use of Copper ore rich in Antimony. Unfortunately none of my information sources mention the use of Antimony in pewter.
Biringuccio was writing in the 1530’s, so we can safely say that Antimony was then in use by Alchemists. This pushes its use back to the early 16th century. Now of course it would be really interesting to know who was actually using it, but it is hard to find real evidence of alchemy from the 15th century. We have some, but it is not very informative, at least not in the way I want.
Or do we?
I have also found a translation of a text about Antimony which purports to have been written by Roger Bacon, called “Tract on the tincture and oil of Antimony”, apparently from a German book published in the 17th century.
http://www.levity.com/alchemy/rbacon2.html
Of course it is not likely to have been written by Roger Bacon, since he was around in the 13th century, and many texts were written by people who wanted to give them false authority and antiquity (It being a general tenet of Alchemy that the ancients had quite a few people who knew the secret, thus old texts were better than new ones), and thus affixed the name of someone like Roger Bacon to them.
Given what I quote Biringuccio as saying above, it is interesting to find that the aforementioned tract says:
“Several poor and common Laborers, when they have prepared the Antimonium thus, have taken one part out, to take care of their expenses, so that they may more easily do the rest of the work and complete it, They then mixed it with one part Salmiac, one part Vitro (alii. Nitro, alii. Titro), one part Rebohat, to cleanse the Corpera, and then proceeded to project this mixture onto a pure Lunam. And if the Luna was one Mark, they found two and a half Loth good gold after separation; sometimes even more. And therewith they had accomplished a work providing for their expenses, so that they might even better expect to attain to the Great Work. And the foolish called this a bringing into the Lunam, but they are mistaken. For such gold is not brought in by the Spiritibus (alii. Speciebus), but any Luna contains two Mark gold to the Loth, some even more. But this gold is united to the Lunar nature to such a degree that it may not be separated from it, neither by Aquafort, nor by common Antimonium, as the goldsmiths know. When however the just mentioned mixture is thrown onto the Lunam in flux, then such a separation takes place that the Luna quite readily gives away her implanted gold either in Aquafort or in Regal, and lets herself separate from it, strikes it to the ground and precipitates it, which would or might otherwise not happen. Therefore it is not a bringing into the Lunam, but a bringing out of the Luna.”
What this looks like to me is a recipe for preparing an Antimonial solution, which when added to Silver makes something that looks like gold. The moon is usually Silver, at least according to my familiarity with Alchemy, gold being called the Sun.
What is more amusing is that on the levity.com website from which the above quote is taken, is mention of “The secret book of Artephius”,
http://www.levity.com/alchemy/artephiu.html
This was allegedly written in the 12th century, and translated by someone called “Lapidus”, who published a book called “In pursuit of Gold” in 1976. Oddly enough, I can find no other mention of Artephius online, except connected to this “In pursuit of gold”, or in other words, this person and manuscript may well not exist. Neither of my two modern books on Alchemy mention Lapidus or Artephius. The book of Artephius apparently describes the use of Antimony to do the usual Alchemical operations.
The mystery becomes farcical when you read this thread from the Levity.com archives, about Lapidus:
http://www.levity.com/alchemy/t_lapid.html
In summary, someone asks if Lapidus is still alive and going to publish something else, and if he is a certain named person. One person replied that he was dead, and not the named person. Someone else then replied that Lapidus was in fact alive, and possibly going to publish another book soon.
This goes to show the confusion that surrounds the modern practise of Alchemy, and the opportunities for fraud and lies. Which is a shame.
Friday, September 14, 2007
What things do I not know much about in Alchemy?
OK, lots of things I don’t know about in Alchemy. Nevertheless, there are couple of questions that I wonder what the answers are.
For starters, there is the change over from mercury to antinomy in the 16th century. At the beginning of the century we have James 4th of Scotland’s pet alchemist buying mercury, and using some gold and other chemicals, but no mention of Antimony. By the beginning of the next century, with the publication of a book called “The triumphal chariot of Alchemy” we have them using Antimony. When and why did that happen?
Moreover we have Newton, (who died in 1727) spending a great deal of time on Alchemy, often locking himself in his room for days at a time and producing copious notes on all the alchemical texts he could find. He produced the Star regulus of Antimony, a crystalline form of antimony. More information can be found here:
http://webapp1.dlib.indiana.edu/newton/reference/chemProd.do
The earliest mention I have of Antimony is in the 12 Keyes of Basil Valentine. Now, according to the preface in a reprinted Llanerch edition of selections from “The Hermetic Museum”, (Itself first published in 1625) Basil Valentine was a Benedictine Monk, and various people place him around the 1490’s. However this is clearly wrong, I will explain why shortly, yet the writer of the preface of my Llanerch edition accepts this personage as being genuine. By contrast, John Read (Through alchemy to Chemistry”, published in 1957, and coincidentally a professor of Chemistry at St Andrews) points out that the first copy of any texts by Basil Valentine are dated to 1599.
The text in question runs:
“Take a fierce grey wolf, which, though on account of its name it be subject to the way of warlike Mars, is by birth the offspring of ancient Saturn, and is found in the valleys and mountains of the world, where he roams about savage with hunger. Cast to him the body of the King, and when he has devoured it, burn him entirely to ashes in a great fire. By this process the King will have been liberated; and when it has been performed thrice the Lion has overcome the wolf and will find nothing more to devour in him. Thus our body has been rendered fit for the first stage of our work.”
Read says that the grey wolf is Antimony Sulphide, or Stibnite, an antimony ore, known as the wolf of the metals because of its ability to unite with all the alchemical metals except gold. The repeated fusion of it with gold could be used as a purifying method for the gold.
Now, what makes me sure that Basil vValentine, or rather whoever was writing under that name (Read suggests that a Johann Tholde, a Frankenhausen salt maker was perhaps the author) was writing in the later 16th century is that he insists upon three elements, Mercury, Sulphur and Salt. This is a Paracelsian formulation. Paracelsus, who died in 1541, is famous for his views of alchemy and chemistry, and I am sure that you have all heard something about him. But anyway, as far as I have read, he is the one who introduced the idea of Salt, as well as the other two, whereas before him alchemists used just Mercury and Sulphur. So this Basil Valentine is most likely a late 16th century person.
This is made clearer by the fact that someone, calling themselves Basil Valentine, wrote “The triumphal Chariot of Antimony”, published in 1604. This, according to Read is probably the first monograph on a chemical element.
This still does not explain why Alchemists started using Antimony. It may be that they had been using it for many years, but somehow, amongst all the confusion of alchemical writings, this has not been noticed. Somehow I doubt that though.
“Chemistry of the elements” an otherwise excellent textbook, falls for the claims of Basil Valentine being around in the 15th century, but has some useful information, viz: stibnite was used as a black eye colouring in Biblical times, and it may be that it was isolated by Albertus Magnus in the early 13th century. There is apparently mention of an antimonium by Jabir in ~800.
When I turn to “De Re Metallica” I find that Antimony is mentioned as being something you can smelt, but there is little detail. We can therefore be sure that it was around as a separate element in the 16th century, but there is little evidence to suggest it was widely known and used before that period.
So I think it reasonable that Alchemists noticed the properties of Antimony some time during the 1500’s, and it found its way into their everyday use, but in which country and decade this was done, and who popularized it, is unknown.
By comparison, in Thomas Norton’s treatise on Alchemy, which is also in “The Hermetic Museum”, is definitely dated to 1477, and although I have not read and understood it fully, it seems to lack reference to Antimony, instead talking about the usual Alchemical Sulphur, Mercury, quicklime, Magnesia and others. It does show that by the late 15th century such people were taking a close interest in operations on all sorts of minerals and metals, which can be seen in fruition in Agricola’s “De Re Metallica” 70 years later.
The annoying thing is that my question is likely never to be answered, due simply to lack of evidence.
The second question I am interested in is the change to a fully internal self development method of philosophy by allegory. By the 17th century this was pretty much complete, Alchemy was divorcing itself from chemistry and was almost wholly magical in a way which it had not been before. Before, there was some relationship to the real world. By the end, there was not, it was all allegorical. It is clear that by the later medieval period Alchemy was splitting up into various strands, from the purely spiritual to the practical, (And separate from all that we had the artisans who worked with material stuff all day refining their techniques and understanding of what things did, even if they didn’t write it down or produce an overarching scientific theory)
*Chemical note on Antimony: Antimony is an element in the same group as Nitrogen. Below Nitrogen we have Phosphorous, Arsenic, Antimony and then Bismuth. The last three are poisonous. Antimony is one step along from Tin, and is a silvery coloured metal like Tin, and has an atomic weight of 121.75. It is thus one of the densest metals that they would have had access to, in increasing weight they had- Silver, Tin, Antimony, Gold, Mercury, lead and Bismuth, and apparently they were casting Bismuth to make type up for early printing presses in the 15th century.
Antimony is used in lead batteries to help stabilize the sheets of lead, bearings, ammunition, and some electronics thingies e.g. diodes.
For starters, there is the change over from mercury to antinomy in the 16th century. At the beginning of the century we have James 4th of Scotland’s pet alchemist buying mercury, and using some gold and other chemicals, but no mention of Antimony. By the beginning of the next century, with the publication of a book called “The triumphal chariot of Alchemy” we have them using Antimony. When and why did that happen?
Moreover we have Newton, (who died in 1727) spending a great deal of time on Alchemy, often locking himself in his room for days at a time and producing copious notes on all the alchemical texts he could find. He produced the Star regulus of Antimony, a crystalline form of antimony. More information can be found here:
http://webapp1.dlib.indiana.edu/newton/reference/chemProd.do
The earliest mention I have of Antimony is in the 12 Keyes of Basil Valentine. Now, according to the preface in a reprinted Llanerch edition of selections from “The Hermetic Museum”, (Itself first published in 1625) Basil Valentine was a Benedictine Monk, and various people place him around the 1490’s. However this is clearly wrong, I will explain why shortly, yet the writer of the preface of my Llanerch edition accepts this personage as being genuine. By contrast, John Read (Through alchemy to Chemistry”, published in 1957, and coincidentally a professor of Chemistry at St Andrews) points out that the first copy of any texts by Basil Valentine are dated to 1599.
The text in question runs:
“Take a fierce grey wolf, which, though on account of its name it be subject to the way of warlike Mars, is by birth the offspring of ancient Saturn, and is found in the valleys and mountains of the world, where he roams about savage with hunger. Cast to him the body of the King, and when he has devoured it, burn him entirely to ashes in a great fire. By this process the King will have been liberated; and when it has been performed thrice the Lion has overcome the wolf and will find nothing more to devour in him. Thus our body has been rendered fit for the first stage of our work.”
Read says that the grey wolf is Antimony Sulphide, or Stibnite, an antimony ore, known as the wolf of the metals because of its ability to unite with all the alchemical metals except gold. The repeated fusion of it with gold could be used as a purifying method for the gold.
Now, what makes me sure that Basil vValentine, or rather whoever was writing under that name (Read suggests that a Johann Tholde, a Frankenhausen salt maker was perhaps the author) was writing in the later 16th century is that he insists upon three elements, Mercury, Sulphur and Salt. This is a Paracelsian formulation. Paracelsus, who died in 1541, is famous for his views of alchemy and chemistry, and I am sure that you have all heard something about him. But anyway, as far as I have read, he is the one who introduced the idea of Salt, as well as the other two, whereas before him alchemists used just Mercury and Sulphur. So this Basil Valentine is most likely a late 16th century person.
This is made clearer by the fact that someone, calling themselves Basil Valentine, wrote “The triumphal Chariot of Antimony”, published in 1604. This, according to Read is probably the first monograph on a chemical element.
This still does not explain why Alchemists started using Antimony. It may be that they had been using it for many years, but somehow, amongst all the confusion of alchemical writings, this has not been noticed. Somehow I doubt that though.
“Chemistry of the elements” an otherwise excellent textbook, falls for the claims of Basil Valentine being around in the 15th century, but has some useful information, viz: stibnite was used as a black eye colouring in Biblical times, and it may be that it was isolated by Albertus Magnus in the early 13th century. There is apparently mention of an antimonium by Jabir in ~800.
When I turn to “De Re Metallica” I find that Antimony is mentioned as being something you can smelt, but there is little detail. We can therefore be sure that it was around as a separate element in the 16th century, but there is little evidence to suggest it was widely known and used before that period.
So I think it reasonable that Alchemists noticed the properties of Antimony some time during the 1500’s, and it found its way into their everyday use, but in which country and decade this was done, and who popularized it, is unknown.
By comparison, in Thomas Norton’s treatise on Alchemy, which is also in “The Hermetic Museum”, is definitely dated to 1477, and although I have not read and understood it fully, it seems to lack reference to Antimony, instead talking about the usual Alchemical Sulphur, Mercury, quicklime, Magnesia and others. It does show that by the late 15th century such people were taking a close interest in operations on all sorts of minerals and metals, which can be seen in fruition in Agricola’s “De Re Metallica” 70 years later.
The annoying thing is that my question is likely never to be answered, due simply to lack of evidence.
The second question I am interested in is the change to a fully internal self development method of philosophy by allegory. By the 17th century this was pretty much complete, Alchemy was divorcing itself from chemistry and was almost wholly magical in a way which it had not been before. Before, there was some relationship to the real world. By the end, there was not, it was all allegorical. It is clear that by the later medieval period Alchemy was splitting up into various strands, from the purely spiritual to the practical, (And separate from all that we had the artisans who worked with material stuff all day refining their techniques and understanding of what things did, even if they didn’t write it down or produce an overarching scientific theory)
*Chemical note on Antimony: Antimony is an element in the same group as Nitrogen. Below Nitrogen we have Phosphorous, Arsenic, Antimony and then Bismuth. The last three are poisonous. Antimony is one step along from Tin, and is a silvery coloured metal like Tin, and has an atomic weight of 121.75. It is thus one of the densest metals that they would have had access to, in increasing weight they had- Silver, Tin, Antimony, Gold, Mercury, lead and Bismuth, and apparently they were casting Bismuth to make type up for early printing presses in the 15th century.
Antimony is used in lead batteries to help stabilize the sheets of lead, bearings, ammunition, and some electronics thingies e.g. diodes.
Monday, April 23, 2007
Colouring glass
Since making my own glass seems very hard to do, I have cheated a bit. With my furnace up around 950 to 1,000 degrees, I can melt normal modern bottle glass. So as a test today I tried to colour some glass, by means of rust.
You see, iron makes glass green in colour. Green glass was produced regularly in England, because they used yellow sand which has a high iron content, as little as 0.5% colouring the glass green. If you wanted really clear glass you had to use white sand or quartz, which were not widely found in the UK, more often found in Germany. However all through the medieval period window glass was imported from the continent.
A somewhat green british glass alembic can be seen here:

(From: http://www.exeter.gov.uk/timetrail/07_middleages/object_detail.asp?photoref=7_89, Exeter during the middle ages)
This is the glass before:
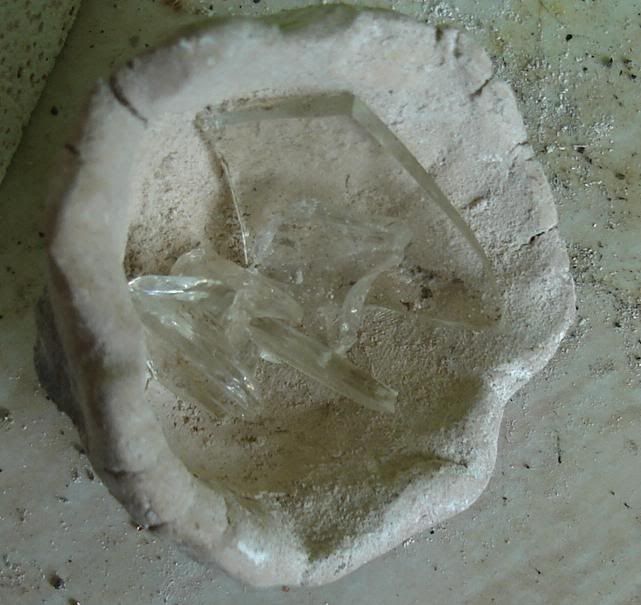
Sitting in a crucible of my own manufacture that has survived at least one firing up to the correct temperature.
So, I melted the glass to a gooey consistency, then dropped some rust on top, and stuck it back in the furnace for ten minutes more. After that time I took it out, partly because I was running out of fuel. The end result was this:
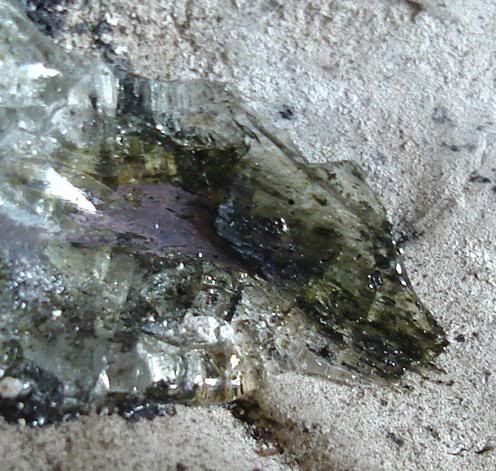
It’s not very exciting, is it? There was not enough time for the iron to diffuse through the glass, and also I had not mixed the metal in properly. Nevertheless a green tint should be visible. This is a fairly simple demonstration that I could carry out at an event without any trouble, especially if I mixed the iron into the glass properly. Moreover, different colours can be had with different additives.
You see, iron makes glass green in colour. Green glass was produced regularly in England, because they used yellow sand which has a high iron content, as little as 0.5% colouring the glass green. If you wanted really clear glass you had to use white sand or quartz, which were not widely found in the UK, more often found in Germany. However all through the medieval period window glass was imported from the continent.
A somewhat green british glass alembic can be seen here:

(From: http://www.exeter.gov.uk/timetrail/07_middleages/object_detail.asp?photoref=7_89, Exeter during the middle ages)
This is the glass before:
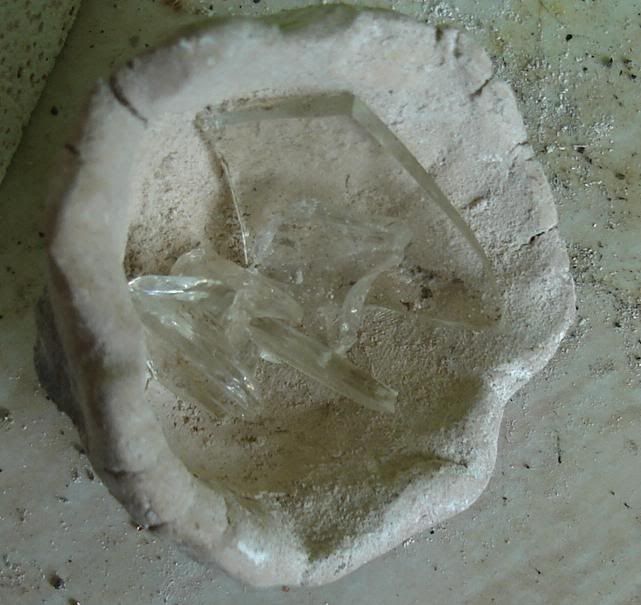
Sitting in a crucible of my own manufacture that has survived at least one firing up to the correct temperature.
So, I melted the glass to a gooey consistency, then dropped some rust on top, and stuck it back in the furnace for ten minutes more. After that time I took it out, partly because I was running out of fuel. The end result was this:
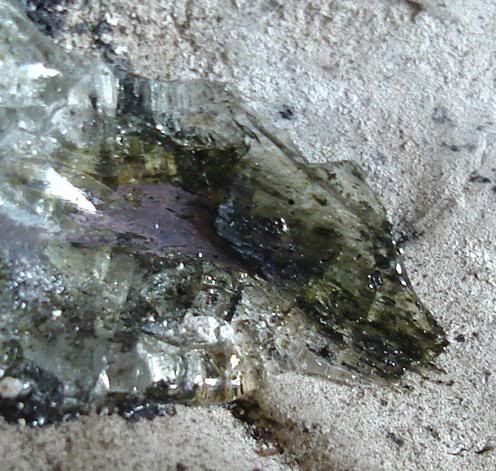
It’s not very exciting, is it? There was not enough time for the iron to diffuse through the glass, and also I had not mixed the metal in properly. Nevertheless a green tint should be visible. This is a fairly simple demonstration that I could carry out at an event without any trouble, especially if I mixed the iron into the glass properly. Moreover, different colours can be had with different additives.
The difficulties of finding original sources (and medieval fire retardant part 3)
Those of you who recall my last experiments making alleged fire retardant will remember that I found information about it in the journal of the Historical Metallurgy society, in an article by Jochem Walters. With regards to the fire retardant he says:
Un-slaked lime has been a component of widely varied fire-proof products throughout the modern period. See the Curioser Kunstler (1 133/257/305/348)
There was an e-mail address at the bottom of the article, so I mailed him a couple of weeks ago, and received a reply.
He said that the Kurioser Kunstler was the largest collection of recipes for all sorts of things, and was published by Johann Kunckel von Loewenstjern, anonymously in Nuremberg in 1696. The full title being „Der Curieusen Kunst- und Werck-Schule
erster und anderer Theil“
Now, Kunst translates roughly as art, and I think a rough translation would read “The curious art and work something something something. (OK, I’m going to have to ask Lukas what this means)
It was translated by Robert Dossie in “The Handmaid to the Arts”, vol. 2, 1750, with various editions published later in the century. Now, it would be really good if I could get a copy of this, unfortunately there are not any I can find online for sale. Apparently they are very rare. But another of his books is available for only £150.
Nobody appears to have re-published it since the 18th century. I am finding this is a very common problem, whether I am after translations of Geber, or some 25th century alchemical works, it seems the last full reprinting was often done in the 17th or 18th centuries. Which is only to be expected, but it means that for someone like me who I only dabbling in it, information is very hard to come by.
Un-slaked lime has been a component of widely varied fire-proof products throughout the modern period. See the Curioser Kunstler (1 133/257/305/348)
There was an e-mail address at the bottom of the article, so I mailed him a couple of weeks ago, and received a reply.
He said that the Kurioser Kunstler was the largest collection of recipes for all sorts of things, and was published by Johann Kunckel von Loewenstjern, anonymously in Nuremberg in 1696. The full title being „Der Curieusen Kunst- und Werck-Schule
erster und anderer Theil“
Now, Kunst translates roughly as art, and I think a rough translation would read “The curious art and work something something something. (OK, I’m going to have to ask Lukas what this means)
It was translated by Robert Dossie in “The Handmaid to the Arts”, vol. 2, 1750, with various editions published later in the century. Now, it would be really good if I could get a copy of this, unfortunately there are not any I can find online for sale. Apparently they are very rare. But another of his books is available for only £150.
Nobody appears to have re-published it since the 18th century. I am finding this is a very common problem, whether I am after translations of Geber, or some 25th century alchemical works, it seems the last full reprinting was often done in the 17th or 18th centuries. Which is only to be expected, but it means that for someone like me who I only dabbling in it, information is very hard to come by.
Monday, March 5, 2007
Medieval fire retardant?
In the last issue of the journal of the Historical Metallurgy society, there was an article on a Byzantine gold smiths manual from the 11th century. Amongst many other things in the manual was a recipe that translated, said:
My attention was caught by this, and I began to wonder what it was and whether it actually worked.
The article’s author only had this to say about the recipe:
Un-slaked lime has been a component of widely varied fire-proof products throughout the modern period. See the Curioser Kunstler (1 133/257/305/348)
Not enough for my curiosity. So I decided to try and replicate the recipe.
Now, at first sight it looks pretty silly. Oil and quicklime? The oil would prevent the quicklime from contact with water, but then if you distilled it with a caustic solution, what you would get might well be a solution of metallic salts, which when put onto cloth would result in, when dried, a layer of metal complex salts that I suppose would retard combustion a bit.
I set up my furnace as below, with the pot containing the ingredients sitting on top of some broken bricks, to raise it above the flames.
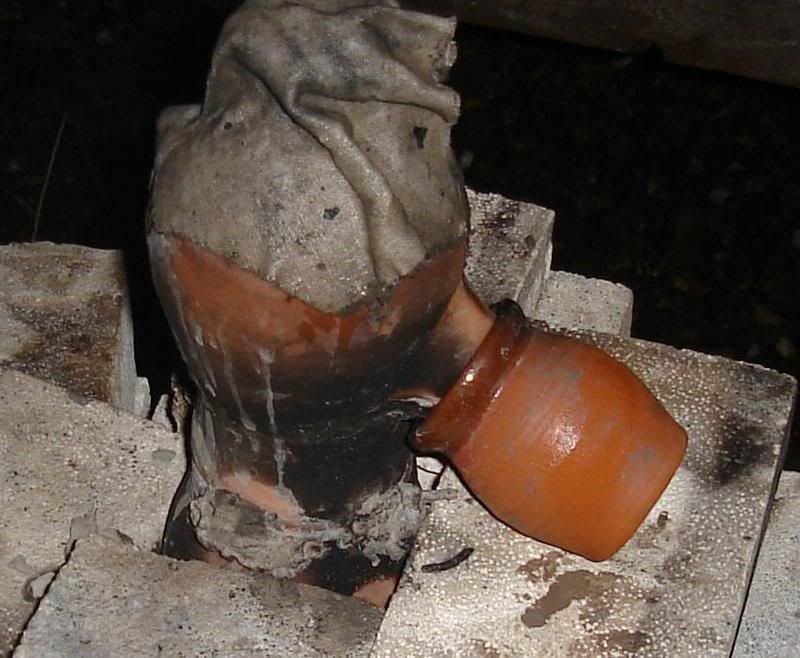
I mixed 30 grams of quicklime with olive oil, being what I had handy. Then I mixed some sodium hydroxide crystals with water, and poured that in as well. It started boiling over pretty quickly after I put it in the flames, and I lost a fair bit of vapour that did not condense out, although it was probably water. After about 20 minutes I stopped the process, and what was left in the bottom of the vessel was a lump of slightly foamed material.
What had come over was liquid, and smelt funny. It was perhaps a little bit more gloopy than I would expect for plain water.
So I dipped several pieces of linen into the liquid and dried them. They all burnt, although just a little bit slower than normal. This was not good, but not unexpected given the uncertain nature of what I was attempting. The recipe says to expose them to the fire after dipping them in the solution, but seeing as you can get the same effects by dipping the cloth in water, I figure that the liquid is supposed to form a coating. After all, a fire retardant coating would be useful on something like an apron, which comes close to a fire regularly, but it would be very impractical to keep it wet all the time.
After some googling and reading up on things, it appears that linseed oil would be the best to use, there being mention of its use in fireproof glue.
(http://www.wholesaleexporter.com/fireproof-glue.htm)
It also seems that anaerobically heating linseed oil to 300C makes it polymerize. I think that such a polymerized oil would not be so easily burnt, and would thus act as a fire retardant. In fact some polymers are sold as fire proof, because they are highly polymerized and their outer layers are already reacted with oxygen during the manufacturing stage, meaning there is nothing that will catch fire, unless you apply so much heat as to break down the polymer chains themselves.
So next time I shall use linseed oil, and boil it for longer at higher temperatures. This should help isolate the exact way this works. Possibly the action of the lime and sodium hydroxide solution is to keep the linseed oil isolated from the atmosphere enough to begin polymerizing. Or maybe not. It is frustratingly unclear.
Another mysterious method
Take unslaked lime, mix oil into the lime, wetting it as thoroughly once or twice. Then pour it into a distillation vessel. Also add a caustic solution [?] whereby you pour it all over until it is 2 fingers deep. Now fill this divine water into another flagon. After that, take a linen cloth and dampen it with this water and expose it to the fire. If the cloth burns, you know that it was not prepared well. Make the lime preparation again with other un-slaked lime and repeat as before until successful, ie until the fabric no longer catches fire.
My attention was caught by this, and I began to wonder what it was and whether it actually worked.
The article’s author only had this to say about the recipe:
Un-slaked lime has been a component of widely varied fire-proof products throughout the modern period. See the Curioser Kunstler (1 133/257/305/348)
Not enough for my curiosity. So I decided to try and replicate the recipe.
Now, at first sight it looks pretty silly. Oil and quicklime? The oil would prevent the quicklime from contact with water, but then if you distilled it with a caustic solution, what you would get might well be a solution of metallic salts, which when put onto cloth would result in, when dried, a layer of metal complex salts that I suppose would retard combustion a bit.
I set up my furnace as below, with the pot containing the ingredients sitting on top of some broken bricks, to raise it above the flames.
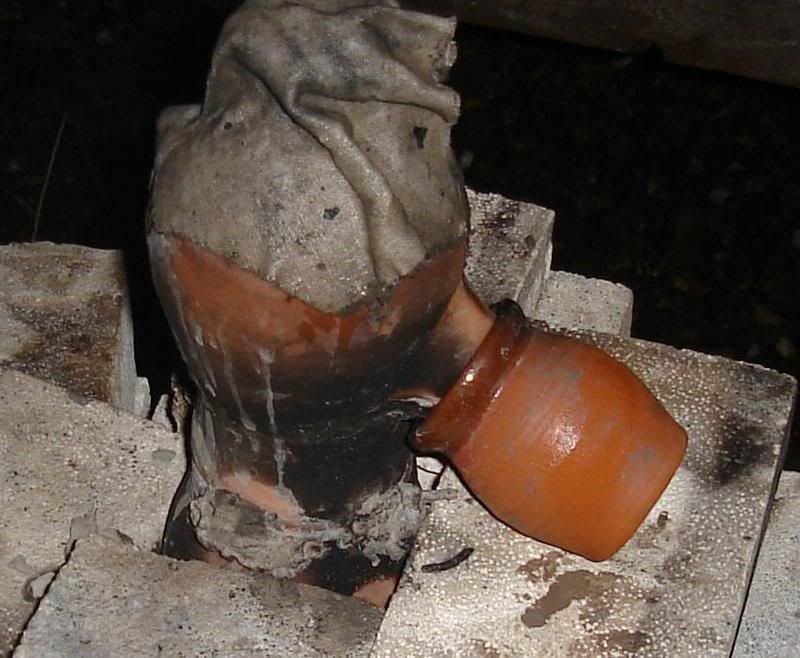
I mixed 30 grams of quicklime with olive oil, being what I had handy. Then I mixed some sodium hydroxide crystals with water, and poured that in as well. It started boiling over pretty quickly after I put it in the flames, and I lost a fair bit of vapour that did not condense out, although it was probably water. After about 20 minutes I stopped the process, and what was left in the bottom of the vessel was a lump of slightly foamed material.
What had come over was liquid, and smelt funny. It was perhaps a little bit more gloopy than I would expect for plain water.
So I dipped several pieces of linen into the liquid and dried them. They all burnt, although just a little bit slower than normal. This was not good, but not unexpected given the uncertain nature of what I was attempting. The recipe says to expose them to the fire after dipping them in the solution, but seeing as you can get the same effects by dipping the cloth in water, I figure that the liquid is supposed to form a coating. After all, a fire retardant coating would be useful on something like an apron, which comes close to a fire regularly, but it would be very impractical to keep it wet all the time.
After some googling and reading up on things, it appears that linseed oil would be the best to use, there being mention of its use in fireproof glue.
(http://www.wholesaleexporter.com/fireproof-glue.htm)
It also seems that anaerobically heating linseed oil to 300C makes it polymerize. I think that such a polymerized oil would not be so easily burnt, and would thus act as a fire retardant. In fact some polymers are sold as fire proof, because they are highly polymerized and their outer layers are already reacted with oxygen during the manufacturing stage, meaning there is nothing that will catch fire, unless you apply so much heat as to break down the polymer chains themselves.
So next time I shall use linseed oil, and boil it for longer at higher temperatures. This should help isolate the exact way this works. Possibly the action of the lime and sodium hydroxide solution is to keep the linseed oil isolated from the atmosphere enough to begin polymerizing. Or maybe not. It is frustratingly unclear.
Friday, March 2, 2007
Calcining lime and ashes
At last, doing what my blog is named after
I bought some garden lime a few weeks ago, which is basically crushed limestone. Limestone is calcium carbonate, CaCO3, and needs to be burnt in order to convert it to CO, calcium oxide, or quicklime. This is caustic (Alkaline), and used for destroying stuff. Also, if you mix it with water in the approved manner, you get lime mortar. Which then, over the years after it has been applied, absorbs CO2 from the air to become calcium carbonate again. All you are doing is making limestone into a form that is easily used for building, and then letting it turn back into limestone once in place.
I need it for several things. To start with, one or two odd chemical recipes require quicklime. (More on them this weekend) Furthermore, I want to see what I can produce and how much and how quickly, to get an idea of lime kilns and their work, and also whether I can make enough to do interesting things with. For example, it would be good to demonstrate making slaked lime (That’s the calcium hydroxide you get by adding water to the calcium oxide) and then using it to stick a couple of stones together.
Today’s take home fact is that lime mortar is re-usable, you just have to burn it.
Procedure:
Take two bits of scrap stainless steel from work. Place lime onto them. Get fire going, and heat up furnace to well over 1,000C. Hold at that temperature for half an hour. Stir lime occasionally. At this stage it should be so hot that any wood you put into the furnace bursts straight into flames.
Working a lime kiln must have been very hot, sweaty work. Holding over 1,000C for days at a time, with mixes of lime and coke or coal or wood tipped in the top would have been hard work. You can still see a lot of limekilns around Scotland, when local supplies of lime were exploited in the 18th and 19th centuries, in order to improve the farmland and build more houses. They are made of brick or stone, and are generally set against a bank or hill in order to make it easy to tip the mix of coal and limestone into the top of the furnace. After some time the material would have sunk to the bottom of the furnace, where I assume it was tapped to allow the lime out, although there would have to be holes to allow air in as well. I cannot find anything useful online about how lime kilns worked.
Regular readers will have noticed my grousing about a lack of reactions between some sand and boiled ashes. So during last week I decided to calcine the ashes I had in order to purify them. The end result was a much smaller amount of brown stuff. They lost 38% of their weight. Now, I am assuming that this was mostly carbon compounds that were oxidized readily in the over 1,000C temperatures that they reached.
The photo below shows the steel sitting in the furnace, which is glowing warmly.
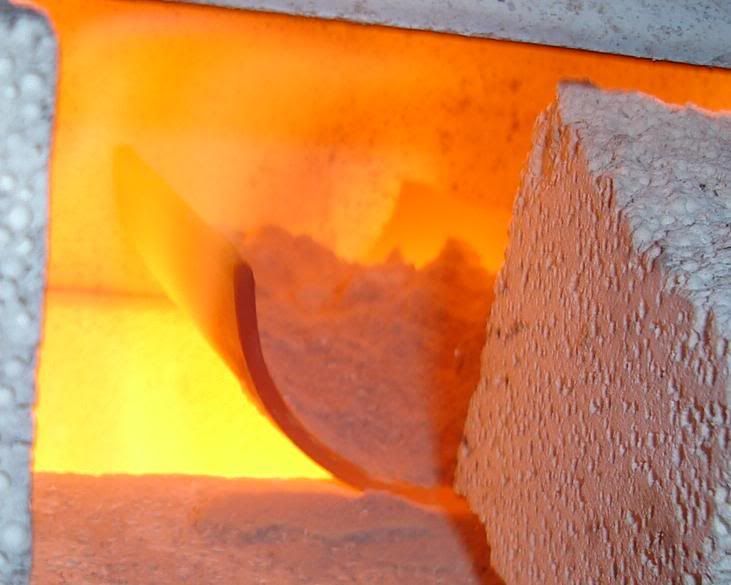
Further information on Lime can be found at these places:
The Scottish Lime centre
Charlestown lime kilns
I bought some garden lime a few weeks ago, which is basically crushed limestone. Limestone is calcium carbonate, CaCO3, and needs to be burnt in order to convert it to CO, calcium oxide, or quicklime. This is caustic (Alkaline), and used for destroying stuff. Also, if you mix it with water in the approved manner, you get lime mortar. Which then, over the years after it has been applied, absorbs CO2 from the air to become calcium carbonate again. All you are doing is making limestone into a form that is easily used for building, and then letting it turn back into limestone once in place.
I need it for several things. To start with, one or two odd chemical recipes require quicklime. (More on them this weekend) Furthermore, I want to see what I can produce and how much and how quickly, to get an idea of lime kilns and their work, and also whether I can make enough to do interesting things with. For example, it would be good to demonstrate making slaked lime (That’s the calcium hydroxide you get by adding water to the calcium oxide) and then using it to stick a couple of stones together.
Today’s take home fact is that lime mortar is re-usable, you just have to burn it.
Procedure:
Take two bits of scrap stainless steel from work. Place lime onto them. Get fire going, and heat up furnace to well over 1,000C. Hold at that temperature for half an hour. Stir lime occasionally. At this stage it should be so hot that any wood you put into the furnace bursts straight into flames.
Working a lime kiln must have been very hot, sweaty work. Holding over 1,000C for days at a time, with mixes of lime and coke or coal or wood tipped in the top would have been hard work. You can still see a lot of limekilns around Scotland, when local supplies of lime were exploited in the 18th and 19th centuries, in order to improve the farmland and build more houses. They are made of brick or stone, and are generally set against a bank or hill in order to make it easy to tip the mix of coal and limestone into the top of the furnace. After some time the material would have sunk to the bottom of the furnace, where I assume it was tapped to allow the lime out, although there would have to be holes to allow air in as well. I cannot find anything useful online about how lime kilns worked.
Regular readers will have noticed my grousing about a lack of reactions between some sand and boiled ashes. So during last week I decided to calcine the ashes I had in order to purify them. The end result was a much smaller amount of brown stuff. They lost 38% of their weight. Now, I am assuming that this was mostly carbon compounds that were oxidized readily in the over 1,000C temperatures that they reached.
The photo below shows the steel sitting in the furnace, which is glowing warmly.
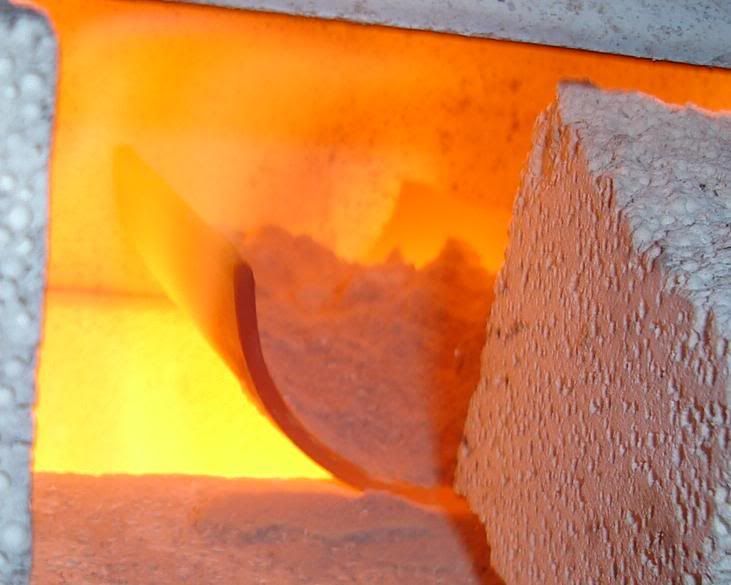
Further information on Lime can be found at these places:
The Scottish Lime centre
Charlestown lime kilns
Sal Alkali and glass making
So, wondering what Sal Alkali is for? Simple- it and quartz sand are all you need to make glass. Oh, and a furnace capable of over 1,000 degrees, maybe a bit more. Have I mentioned that I like working with fire?
What I have done over the past few weeks was produce alkaline powder by burning beech wood. (see previous posts about this and sourcing the wood) Theophilus says to use ashes, but I wanted to see how much salt I could produce, since by the early 16th century glassmakers were certainly making the salt, rather than just using ashes. This has the advantage of meaning you have more control over the glass and what is in it, since simply using the ashes means you can end up with bits of earth and suchlike from the original material, such as bracken roots. (See previous post)
The end result was, not a lot of salt.
I faithfully took the ashes, and boiled them up in a pot, until they were dry, and had turned into a fine gray powder. This powder tested at a pH of about 10, so definitely had some caustic properties in it. I suspect it has a mix of sodium and potassium salts as well as bits of charcoal and other things.
So, to make glass, I weighed out 20grams of ordinary sand with 10 grams of the salt I had previously made. I mixed it up as much as possible, then placed it in the pot you can see in the picture below:
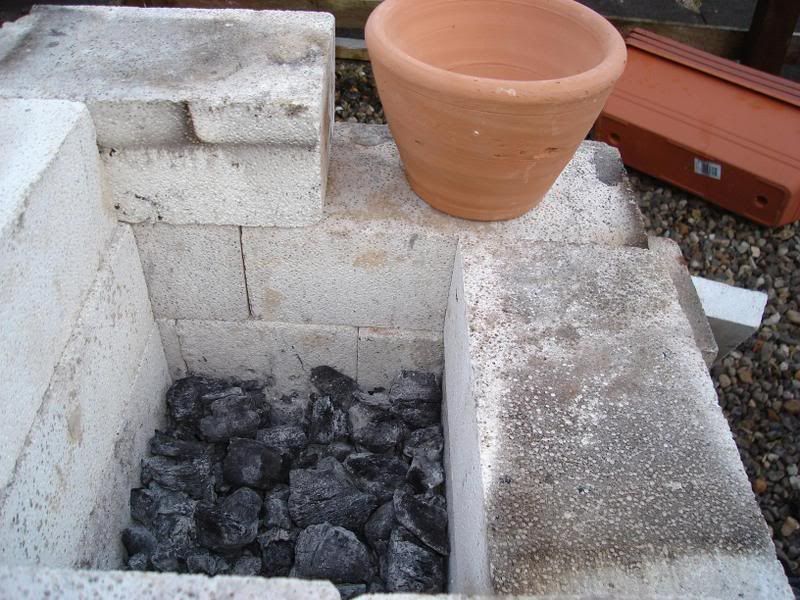
The furnace was set up with a 2 brick deep volume for the charcoal, and the bellows in their usual place. Then, with it lit, I bellowed it up to over 1,000C in an hour or so. It takes a long time to reach thermal equilibrium between the inside and outside of the furnace. With the crucible inside, and glowing red, I held it at 1030-1050 for 10 minutes, and stirred the sand/ salts mix occasionally. It definitely fizzed a little around the thousand mark, and oddly enough potassium carbonate melts at 980C…
This photo shows the pot in use:
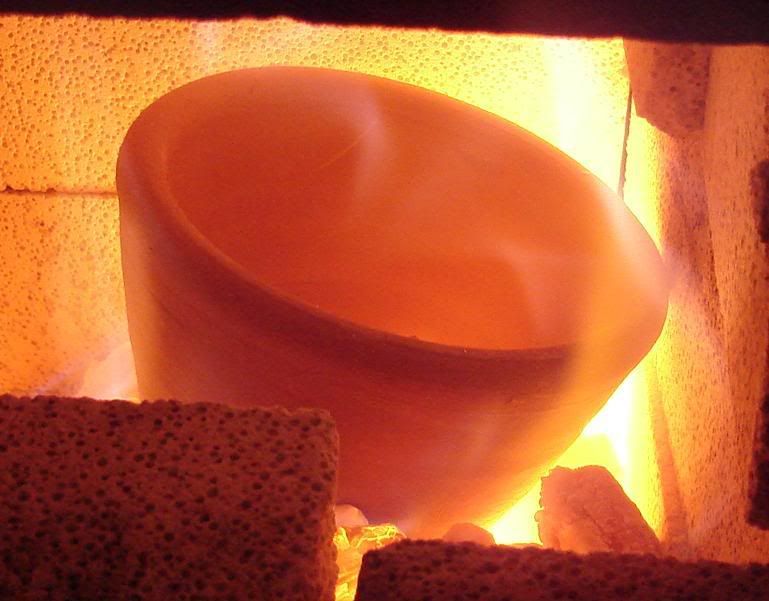
The problem was that the pot actually cracked during use. It has since split into several parts, and it is clear that it is too thick, and could not cope with the different heating rates of different parts of the pot. Fortunately I did not lose any of the fritted mixture.
In this photo you can see the two ingredients and what they combined to make. The sand is at the top, the boiled ashes to the bottom right, and the fritted material to the bottom left. It doesn’t look very good I am afraid.
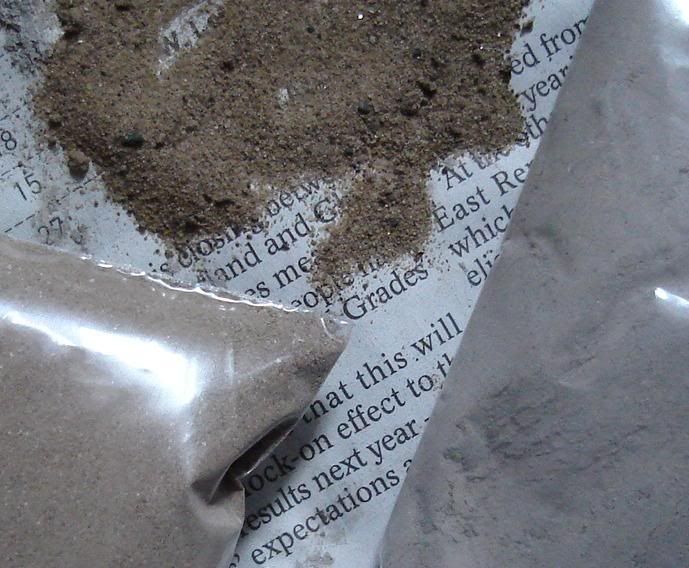
Next time I shall heat it up to over 1,000C, and mix in more boiled ashes. I suspect that the percentage of sodium and potassium salts might not be high enough, so if I mix more in I stand a better chance of getting the sand to melt. The salts melt at a lower temperature and act as a flux, taking the sand (silica) into solution at a much lower temperature. Otherwise I would have to go to at least 1600C for silica to melt. Which is impossible with my set up.
Next time I shall hopefully get a nice blob of glass.
What I have done over the past few weeks was produce alkaline powder by burning beech wood. (see previous posts about this and sourcing the wood) Theophilus says to use ashes, but I wanted to see how much salt I could produce, since by the early 16th century glassmakers were certainly making the salt, rather than just using ashes. This has the advantage of meaning you have more control over the glass and what is in it, since simply using the ashes means you can end up with bits of earth and suchlike from the original material, such as bracken roots. (See previous post)
The end result was, not a lot of salt.
I faithfully took the ashes, and boiled them up in a pot, until they were dry, and had turned into a fine gray powder. This powder tested at a pH of about 10, so definitely had some caustic properties in it. I suspect it has a mix of sodium and potassium salts as well as bits of charcoal and other things.
So, to make glass, I weighed out 20grams of ordinary sand with 10 grams of the salt I had previously made. I mixed it up as much as possible, then placed it in the pot you can see in the picture below:
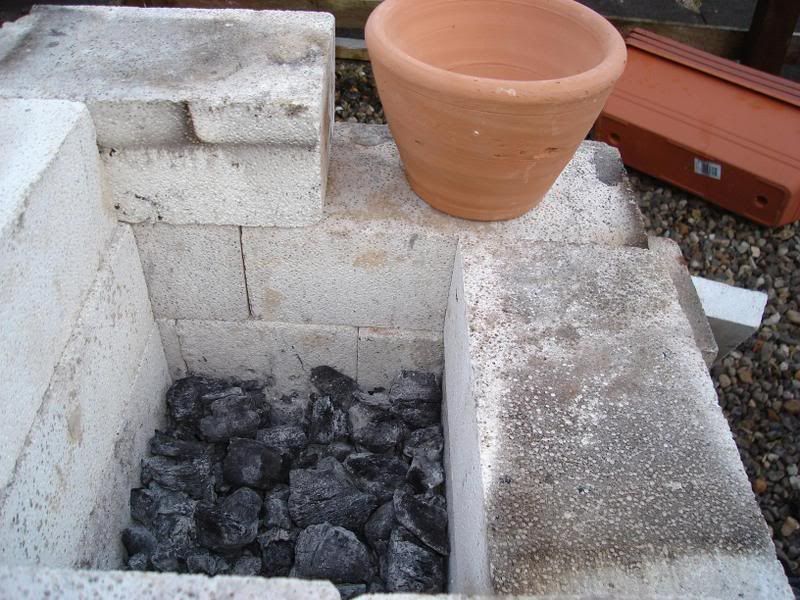
The furnace was set up with a 2 brick deep volume for the charcoal, and the bellows in their usual place. Then, with it lit, I bellowed it up to over 1,000C in an hour or so. It takes a long time to reach thermal equilibrium between the inside and outside of the furnace. With the crucible inside, and glowing red, I held it at 1030-1050 for 10 minutes, and stirred the sand/ salts mix occasionally. It definitely fizzed a little around the thousand mark, and oddly enough potassium carbonate melts at 980C…
This photo shows the pot in use:
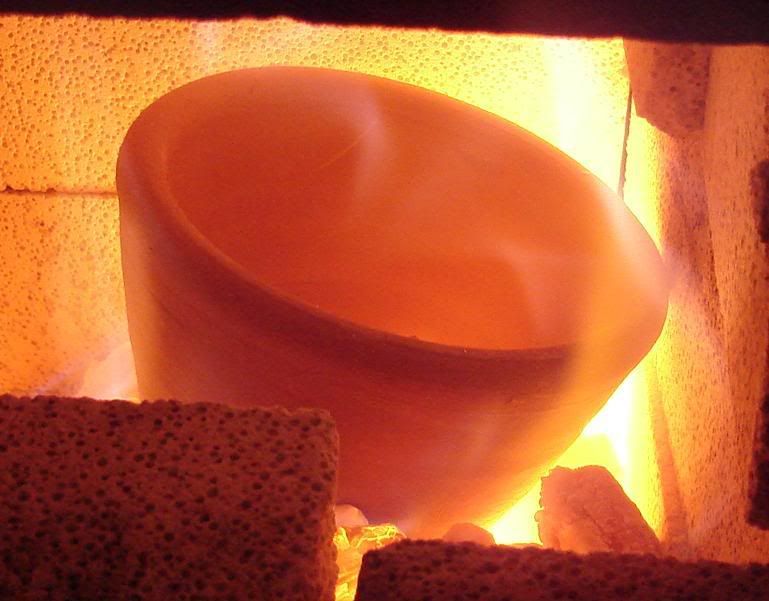
The problem was that the pot actually cracked during use. It has since split into several parts, and it is clear that it is too thick, and could not cope with the different heating rates of different parts of the pot. Fortunately I did not lose any of the fritted mixture.
In this photo you can see the two ingredients and what they combined to make. The sand is at the top, the boiled ashes to the bottom right, and the fritted material to the bottom left. It doesn’t look very good I am afraid.
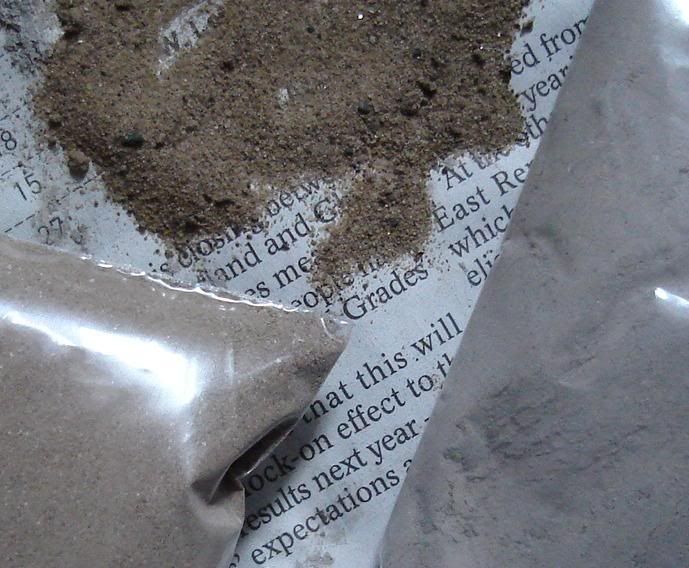
Next time I shall heat it up to over 1,000C, and mix in more boiled ashes. I suspect that the percentage of sodium and potassium salts might not be high enough, so if I mix more in I stand a better chance of getting the sand to melt. The salts melt at a lower temperature and act as a flux, taking the sand (silica) into solution at a much lower temperature. Otherwise I would have to go to at least 1600C for silica to melt. Which is impossible with my set up.
Next time I shall hopefully get a nice blob of glass.
What should I make and do for demonstrating medieval technology?
Any ideas? I have quite a lot of possibilities, involving various amounts of preparation and materials and explanation.
For starters, I could make Gold. Either mosaic gold, which may or may not require the use of mercury. Or I could tin plate lead. Or I could colour silver to make it look like gold, using either distilled eggs or a solution of sulphur and lime that apparently colours copper or silver yellow.
Then I could make some acid- nitric, HCl, Sulphuric. There is quite a list, but the problem is in demonstrating their uses, especially since I do not have any gold to experiment upon. I can mix them with some limestone, which would fizz satisfactorily.
I could distill eggs again. That would get me funny looks, but isn’t very entertaining except to hardened geeks. On the other hand small slow drips of yellow falling into a pot do catch peoples attention. It would be a good lead in to a discussion on the topic of early alchemy though.
Casting metals is also a good one, I have yet to see someone do that at an event. I intend to be the first. (At least in medieval circles that I am in)
There are so many things to be made, from thimbles up to spurs, or belt buckles, and large objects like a mortar and pestle, and candlesticks. I have not seen many people with medieval candlesticks, however they would be expensive in terms of material, and also time to make the mould and then cast the metal into it. (Also, you wouldn’t actually carry them around with you on campaign.) Nevertheless, they are what I aspire to do.
Simpler things can be made using pewter, also including belt studs, buckles, plates, tankards etc.
Of course, I would have to keep people a sensible distance away, at least 3 feet I think. As long as it is small amounts of metal I am dealing with, avoid moisture etc, there is little danger.
Faking coins. What I envisage is this:
I am sitting at my furnace, with a few silver coins of the period of the event. I also have a clay mould of said coins, which I show to the crowd. I then cut up one of the coins, put about 2/3 of it into a crucible with some copper or tin to make up the weight, then melt it, and cast it into the clay. By doing this several times I can end up with more silver than I started with, and more coins, thus netting more money. Once I crack the mould open, I pass the fake coin round, but my assistant will have nipped out the back to get some people pretending to be the local law officers. I will scarper out the back just before the law gets there, who will then arrest the MoP holding the fake coin, for counterfeiting, and lead them away, possibly explaining loudly to the crowd the punishments for counterfeiting.
I like it. Entertaining and educational, all in one go. I know who to get the coins from as well, I have plenty of copper and can get some silver.
I could also do some glassmaking of small things, like glass phials or beads. This would only be tricky insofar as the weather would have to be good and a lot of heat would be required. It would however be do-able, since it appears that the melting point of potash and sand based glass is around 1,000C, which my furnace can easily reach. There are also the health and safety aspects of trying to blow glass, especially in front of people.
On a more industrial scale, it would be easy to make quicklime. I would set up my furnace like a chimney, and pile in limestone and charcoal. It would however smell a lot, necessitating a large field, and a strong wind to take the pollution away. The same goes for ore smelting. I could roast copper ores to remove the sulphur, smelt iron ore using charcoal, ore and limestone. In fact the latter has already been done at Rivaulx abbey:
Iron ore smelting
It would be nice to repeat it. I do know one or two people with spare fields.
The tricky bits
Apart from all the fun stuff, the other problem is holding the crowd’s attention. Now, I don’t expect them to be 8 deep around me, but I have to be able to hold peoples attention whilst doing preparation for my experiments. This may mean I need an assistant to do some stuff and hand me some tools and equipment as I need them. I shall probably require a bellow monkey, to be paid either with beer or whatever else comes handy. Failing that I need a pyromaniac whose content to watch the flames all day and pump up the heat when necessary. I’m sure there are one or two of them around.
Several of my experiments or demos can be done at once. For example, I could start something distilling on top of the furnace, after having put on some metal to melt in the furnace, and when all that is going on, I can be moulding some clay, or grinding something up. This would keep me always busy doing something, so that the passing MoPs might see something they are interested in. The drawback is that MoPs are often very shy. If you are busy, many of them will not interrupt, except the annoying ones with stupid questions. So I need to have ways of opening it all up to them, so they can ask questions.
The other way of doing it is to have a lecture of some sort (obviously not the same kind as at school) where I show people things. For example, I can have half made clay moulds for showing people, as well as used ones, and the raw materials for making them. This would be easy enough to do, and keep them interested for the 5 or 10 minutes necessary before something else happens. The same thing can be done with some raw material, eg uncovering it and explaining how it is made. I could scrape the Spanish green off copper whilst something is distilling in the background, for example.
Another approach related to lecturing might be to set specific times when I will be doing something, such as casting a hand bell at 11am. This would enable people to gather to watch, and save me having to start and perhaps stop activity at odd times. All this would require is a friendly events organizer including me on the program, or a chalkboard somewhere obvious with timings on it. I would start with a general introduction, show of tools and materials, and get stuck in, hopefully with them asking questions as I work.
Each approach has its ups and downs, and to be honest, I shall be winging it at first. Writing specific plans shall be left until after I have some experience to back up my opinions. Outlines however are useful for jogging the memory, and I shall be writing them in my medieval notebook, using a quill pen. In fact this post is an outline, written to solicit comments on what I might be better off doing.
For starters, I could make Gold. Either mosaic gold, which may or may not require the use of mercury. Or I could tin plate lead. Or I could colour silver to make it look like gold, using either distilled eggs or a solution of sulphur and lime that apparently colours copper or silver yellow.
Then I could make some acid- nitric, HCl, Sulphuric. There is quite a list, but the problem is in demonstrating their uses, especially since I do not have any gold to experiment upon. I can mix them with some limestone, which would fizz satisfactorily.
I could distill eggs again. That would get me funny looks, but isn’t very entertaining except to hardened geeks. On the other hand small slow drips of yellow falling into a pot do catch peoples attention. It would be a good lead in to a discussion on the topic of early alchemy though.
Casting metals is also a good one, I have yet to see someone do that at an event. I intend to be the first. (At least in medieval circles that I am in)
There are so many things to be made, from thimbles up to spurs, or belt buckles, and large objects like a mortar and pestle, and candlesticks. I have not seen many people with medieval candlesticks, however they would be expensive in terms of material, and also time to make the mould and then cast the metal into it. (Also, you wouldn’t actually carry them around with you on campaign.) Nevertheless, they are what I aspire to do.
Simpler things can be made using pewter, also including belt studs, buckles, plates, tankards etc.
Of course, I would have to keep people a sensible distance away, at least 3 feet I think. As long as it is small amounts of metal I am dealing with, avoid moisture etc, there is little danger.
Faking coins. What I envisage is this:
I am sitting at my furnace, with a few silver coins of the period of the event. I also have a clay mould of said coins, which I show to the crowd. I then cut up one of the coins, put about 2/3 of it into a crucible with some copper or tin to make up the weight, then melt it, and cast it into the clay. By doing this several times I can end up with more silver than I started with, and more coins, thus netting more money. Once I crack the mould open, I pass the fake coin round, but my assistant will have nipped out the back to get some people pretending to be the local law officers. I will scarper out the back just before the law gets there, who will then arrest the MoP holding the fake coin, for counterfeiting, and lead them away, possibly explaining loudly to the crowd the punishments for counterfeiting.
I like it. Entertaining and educational, all in one go. I know who to get the coins from as well, I have plenty of copper and can get some silver.
I could also do some glassmaking of small things, like glass phials or beads. This would only be tricky insofar as the weather would have to be good and a lot of heat would be required. It would however be do-able, since it appears that the melting point of potash and sand based glass is around 1,000C, which my furnace can easily reach. There are also the health and safety aspects of trying to blow glass, especially in front of people.
On a more industrial scale, it would be easy to make quicklime. I would set up my furnace like a chimney, and pile in limestone and charcoal. It would however smell a lot, necessitating a large field, and a strong wind to take the pollution away. The same goes for ore smelting. I could roast copper ores to remove the sulphur, smelt iron ore using charcoal, ore and limestone. In fact the latter has already been done at Rivaulx abbey:
Iron ore smelting
It would be nice to repeat it. I do know one or two people with spare fields.
The tricky bits
Apart from all the fun stuff, the other problem is holding the crowd’s attention. Now, I don’t expect them to be 8 deep around me, but I have to be able to hold peoples attention whilst doing preparation for my experiments. This may mean I need an assistant to do some stuff and hand me some tools and equipment as I need them. I shall probably require a bellow monkey, to be paid either with beer or whatever else comes handy. Failing that I need a pyromaniac whose content to watch the flames all day and pump up the heat when necessary. I’m sure there are one or two of them around.
Several of my experiments or demos can be done at once. For example, I could start something distilling on top of the furnace, after having put on some metal to melt in the furnace, and when all that is going on, I can be moulding some clay, or grinding something up. This would keep me always busy doing something, so that the passing MoPs might see something they are interested in. The drawback is that MoPs are often very shy. If you are busy, many of them will not interrupt, except the annoying ones with stupid questions. So I need to have ways of opening it all up to them, so they can ask questions.
The other way of doing it is to have a lecture of some sort (obviously not the same kind as at school) where I show people things. For example, I can have half made clay moulds for showing people, as well as used ones, and the raw materials for making them. This would be easy enough to do, and keep them interested for the 5 or 10 minutes necessary before something else happens. The same thing can be done with some raw material, eg uncovering it and explaining how it is made. I could scrape the Spanish green off copper whilst something is distilling in the background, for example.
Another approach related to lecturing might be to set specific times when I will be doing something, such as casting a hand bell at 11am. This would enable people to gather to watch, and save me having to start and perhaps stop activity at odd times. All this would require is a friendly events organizer including me on the program, or a chalkboard somewhere obvious with timings on it. I would start with a general introduction, show of tools and materials, and get stuck in, hopefully with them asking questions as I work.
Each approach has its ups and downs, and to be honest, I shall be winging it at first. Writing specific plans shall be left until after I have some experience to back up my opinions. Outlines however are useful for jogging the memory, and I shall be writing them in my medieval notebook, using a quill pen. In fact this post is an outline, written to solicit comments on what I might be better off doing.
Saturday, February 10, 2007
A quick note on sources
I have been bandying various names around without giving much information about where they are from. So I shall provide some more information here, and ISBN numbers.
To start with, we have Theophilus, “On divers arts”
This was a manuscript, made up of 3 books, from the 12th century AD. The evidence available suggests they were written by Roger of Helmarshausen, a Benedictine monk working around 1100 onwards in Germany.
The edition I have is the Dover edition, ISBN – 0-486-23784-2, paperback, translated by John G Hawthorne and Cyril Stanley Smith in 1963.
The book is made up of thee books, on the subjects of painting, glass and metalwork. Each book is laid out clearly, starting with the materials necessary to get started, for example, the chapter on glass starts with building the furnace necessary, and near the end has instructions on making lead cames to hold the window together.
The instructions can be fairly readily understood, certainly they are not really inferior to some of the experimental instructions I came across in my chemistry degree.
Then there is “De Re Metallica” by Georgius Agricola. This is the first real treatise employing what we would nowadays think of as the sensible techniques of observation and personal experience, covering areas of mining work, metal working, and mineralogy. This is again a Dover edition, ISBN 0-486-60006-8, translated by Herbert Clark Hoover and Lou Henry Hoover. Yes, it was translated by a former president of the USA. Were that all current and former presidents were as useful and widely interested.
The importance of the book, first printed in 1556, was such that it remained the only authoritative work in the area of mining, according to the blurb on the back. That is some reccomendation.
Next is “De Pirotechnia” of Vannoccio Biringuccio. This was published in 1540, earlier than Agricola, but although it covers some of the same ground, it is less based upon observation, and also has less detail, thus its importance was less. On the other hand the blurb on the back describes it as the first clear, comprehensive work on metallurgy. But for some reason you hear less about Biringuccio, despite it being quite a handy wee book, and for what I am doing, is actually more useful.
My edition is another Dover one, ISBN 0-486-26134-4, translated by Cyril Stanley Smith and Matha Teach Gnudi, who translated it from Italian, Biringuccio being Siennese.
Finally, we have “Il libro dell’Arte” by Cennino d’Andrea Cennini, translated by Daniel V. Thompson, jr. Another Dover book, ISBN 0-486-20054-X. This book is about painting, as written by Cennini in 15th century Florence (According to the back cover. A more modern information source cites it as written in 1390). As such it is not much related to what I am doing, but will likely be useful as a short reference work and to give a better idea of what people were doing with materials in the later medieval period, not to mention it being another book which gives proper, useful instructions that a modern artist should be capable of understanding.
The first 3 are the main books I am relying on for first hand evidence of medieval technology. It is a shame that we do not have much from the 14th and 15th centuries.
The four books are also treasure troves of information in the form of footnotes on many pages, put in by the translators. These help clarify odd bits in the text, and will sometimes wander off at a historical tangent, and discuss all the techniques for manufacture of vitriol, for example. Without them my understanding would be much less.
There are various alchemical texts know from all through the medieval period, however they are by their nature not very informative, and translations are difficult to come by. I would need to find back copies of the journal “Ambix”, published by The Society for the History of Alchemy and Chemistry. Their url is:
There are various alchemical texts know from all through the medieval period, however they are by their nature not very informative, and translations are difficult to come by. I would need to find back copies of the journal “Ambix”, published byThe Society for the History of Alchemy and Chemistry
They have been on the go for decades, and built up a good lot of knowledge.
My main source on Alchemy just now has been “The Alchemists” by F Sherwood Taylor. Published in 1952, ISBN 586 08224 7, its author was Director of the Science Museum and honorary editor of Ambix, the journal of the aforementioned Society for the History of Alchemy and Chemistry. See how important the society is?
I also have a similar book by A J Holmyard, but can’t find it just now.
Another important (to me anyway) organization is The Historical Metallurgy Society, which can be found here:
http://hist-met.org/
I joined the society last year, and in its journal, volume 40 part one for 2006, found a translation of an 11th century text, written by a Greek, called “On the Noble and Illustrious Art of the Goldsmith”. Its an interesting article, since it also covers some ways of making metal objects look like gold, as well as alloying of gold with various metals.
Plus, an even bigger bonus is that the article comes with a list of texts that mention goldsmithing and things to do with metals. The list goes from the circa 1370BC Amarna tablets, via Theophrastus in 305BC, Zosimos, some Arabs, Theophilus, Geber, Biringuccio and up to some anonymous 18th century texts.
I have also purchased a number of back issues of their journals, which have been really informative on the subject of metal working through the ages.
Finally, on alchemy, there are many websites around. Most look really dodgy, full of strange pseudo religious philosophical mumbo-jumbo, or new age wishful thinkin. This one at least has a wider coverage and doesn’t seem to sit in judgement on it all:
http://www.levity.com/alchemy/physical.html
It contains many articles, some translations, much of the history of Alchemy etc. There is so much there that I do not know my way around it yet.
To sum up- there is a fair bit of information out there, it is just hard to find. Everyone on the internet has heard of X, and knows of Y, but for reasons of accuracy and knowledge I need to have the original sources. Internet sources are not always to be trusted. But getting hold of proper academic works and historical texts is hard, but nowadays a lot easier than in the early days of re-enacting. But now I have enough information to get on with things, and I will do so this very weekend.
To start with, we have Theophilus, “On divers arts”
This was a manuscript, made up of 3 books, from the 12th century AD. The evidence available suggests they were written by Roger of Helmarshausen, a Benedictine monk working around 1100 onwards in Germany.
The edition I have is the Dover edition, ISBN – 0-486-23784-2, paperback, translated by John G Hawthorne and Cyril Stanley Smith in 1963.
The book is made up of thee books, on the subjects of painting, glass and metalwork. Each book is laid out clearly, starting with the materials necessary to get started, for example, the chapter on glass starts with building the furnace necessary, and near the end has instructions on making lead cames to hold the window together.
The instructions can be fairly readily understood, certainly they are not really inferior to some of the experimental instructions I came across in my chemistry degree.
Then there is “De Re Metallica” by Georgius Agricola. This is the first real treatise employing what we would nowadays think of as the sensible techniques of observation and personal experience, covering areas of mining work, metal working, and mineralogy. This is again a Dover edition, ISBN 0-486-60006-8, translated by Herbert Clark Hoover and Lou Henry Hoover. Yes, it was translated by a former president of the USA. Were that all current and former presidents were as useful and widely interested.
The importance of the book, first printed in 1556, was such that it remained the only authoritative work in the area of mining, according to the blurb on the back. That is some reccomendation.
Next is “De Pirotechnia” of Vannoccio Biringuccio. This was published in 1540, earlier than Agricola, but although it covers some of the same ground, it is less based upon observation, and also has less detail, thus its importance was less. On the other hand the blurb on the back describes it as the first clear, comprehensive work on metallurgy. But for some reason you hear less about Biringuccio, despite it being quite a handy wee book, and for what I am doing, is actually more useful.
My edition is another Dover one, ISBN 0-486-26134-4, translated by Cyril Stanley Smith and Matha Teach Gnudi, who translated it from Italian, Biringuccio being Siennese.
Finally, we have “Il libro dell’Arte” by Cennino d’Andrea Cennini, translated by Daniel V. Thompson, jr. Another Dover book, ISBN 0-486-20054-X. This book is about painting, as written by Cennini in 15th century Florence (According to the back cover. A more modern information source cites it as written in 1390). As such it is not much related to what I am doing, but will likely be useful as a short reference work and to give a better idea of what people were doing with materials in the later medieval period, not to mention it being another book which gives proper, useful instructions that a modern artist should be capable of understanding.
The first 3 are the main books I am relying on for first hand evidence of medieval technology. It is a shame that we do not have much from the 14th and 15th centuries.
The four books are also treasure troves of information in the form of footnotes on many pages, put in by the translators. These help clarify odd bits in the text, and will sometimes wander off at a historical tangent, and discuss all the techniques for manufacture of vitriol, for example. Without them my understanding would be much less.
There are various alchemical texts know from all through the medieval period, however they are by their nature not very informative, and translations are difficult to come by. I would need to find back copies of the journal “Ambix”, published by The Society for the History of Alchemy and Chemistry. Their url is:
There are various alchemical texts know from all through the medieval period, however they are by their nature not very informative, and translations are difficult to come by. I would need to find back copies of the journal “Ambix”, published byThe Society for the History of Alchemy and Chemistry
They have been on the go for decades, and built up a good lot of knowledge.
My main source on Alchemy just now has been “The Alchemists” by F Sherwood Taylor. Published in 1952, ISBN 586 08224 7, its author was Director of the Science Museum and honorary editor of Ambix, the journal of the aforementioned Society for the History of Alchemy and Chemistry. See how important the society is?
I also have a similar book by A J Holmyard, but can’t find it just now.
Another important (to me anyway) organization is The Historical Metallurgy Society, which can be found here:
http://hist-met.org/
I joined the society last year, and in its journal, volume 40 part one for 2006, found a translation of an 11th century text, written by a Greek, called “On the Noble and Illustrious Art of the Goldsmith”. Its an interesting article, since it also covers some ways of making metal objects look like gold, as well as alloying of gold with various metals.
Plus, an even bigger bonus is that the article comes with a list of texts that mention goldsmithing and things to do with metals. The list goes from the circa 1370BC Amarna tablets, via Theophrastus in 305BC, Zosimos, some Arabs, Theophilus, Geber, Biringuccio and up to some anonymous 18th century texts.
I have also purchased a number of back issues of their journals, which have been really informative on the subject of metal working through the ages.
Finally, on alchemy, there are many websites around. Most look really dodgy, full of strange pseudo religious philosophical mumbo-jumbo, or new age wishful thinkin. This one at least has a wider coverage and doesn’t seem to sit in judgement on it all:
http://www.levity.com/alchemy/physical.html
It contains many articles, some translations, much of the history of Alchemy etc. There is so much there that I do not know my way around it yet.
To sum up- there is a fair bit of information out there, it is just hard to find. Everyone on the internet has heard of X, and knows of Y, but for reasons of accuracy and knowledge I need to have the original sources. Internet sources are not always to be trusted. But getting hold of proper academic works and historical texts is hard, but nowadays a lot easier than in the early days of re-enacting. But now I have enough information to get on with things, and I will do so this very weekend.
Manufacture of clay moulds for casting
I have been itching to start casting bronze or brass. However I could not decide what to make. Fortunately I am getting quite a large collection of pictures of medieval objects, and I settled upon thimbles to start off with. Small and fiddly, but then I would not have to melt too much metal. I could also experiment with the best mixture of clay and other ingredients. This is where it gets tricky.
Making moulds out of clay for objects is annoyingly poorly described. No doubt each master had his own specific recipes; these would probably vary by geography given the availability of local ingredients. Biringuccio, in his “Pirotechnia”, from 1540, is quite specific about all this. He says:
“There are many kinds and varieties of earth that are used for the loam compositions for making the moulds for casting bronze, brass, or other metals. Since this is a very necessary thing, you must try to have the best kind and one that resists the fire well. It must be disposed to receive the metals well, must make a neat casting, and must not shrink or break with cracks on drying or baking. Aside from actual trial, I believe that there is little that can help you, since the clay in itself has no colour or visible sign that I know of to show how satisfactory it is.”
Or in other words, whether it is red, or yellow, or brown, it is not clear as to exactly what kind of clay you should use, but the final product will be obviously good or bad. Difficulties of knowing exactly what to use are compounded by the fact that there is a translators note at the bottom of the page:
“Terra this word was used for earthy materials in general as well as specifically for clay such as used in moulding. We have used either earth or clay as seemed best fitted to the context.”
Or in other words, is Biringuccio talking about earth with much organic material in it, or just for clay? How much sand is in it? Further on he talks about using wool cloth clippings, wool cardings, and sand, iron scale, crushed brick, horse or donkey dung and a variety of other materials. All of these would add some strength to the clay, assuming we are talking about pure clay here. This pure clay would have to be smooth and lacking in lumps and bits of stone, in order to avoid voids and weak spots in the mould. This is easy for me to get nowadays, but much harder for people in the past. Also Biringuccio says it should not be unctuous or lean, characteristics that are somewhat unclear in the context of a book. Perhaps with samples in front of me they would make perfect sense. Also, he appears not to like the use of pure clay, saying “In conclusions, with the exception of pure clay (which is too viscous and tenacious), any other earth, if free from pebbles, could easily serve you by tempering it with others, or if it should have pebbles, by separating them out.”
Biringuccio was greatly enamoured of wool clippings for helping the clay stay good and strong. They would act like a composite, giving greater strength through having these small fibres running through the clay. But there is nothing about how long they would be. I suspect they would be a few mm, but it is not clear. So I shall have to experiment.
I cut up some wool I gathered from fences and ended up with fibres 2 or 3mm long. Together with fine grained sand from the local sandpit, and and buff clay, with a bit of charcoal and some of the strange ashes you get from charcoal briquettes. (Charcoal briquettes are rubbish for my purposes, since they do not burn fast enough.) I have no idea if anything is special about buff clay, but it seems to work, and some googling suggests it is good for modelling etc.
Clay is sticky stuff when wet. I had trouble getting it to stop sticking to my fingers, next time I shall use much dryer clay. Again, from the old books it is not clear how wet it should be. I managed to make two kinds of mould for thimbles. The first, is made of two parts. The aim was to have a top, with a lump sticking down from it to fill in the hollow in the bottom part. This kind of worked, but I forgot to put in the pouring holes so shall have to drill them out. The second kind was made of a hollow, with a lump placed into the middle of it. The aim was to mimic medieval thimbles. The earlier kind, that the second mould is made for, had a hole in the top. Now, I have yet to find any mention of why this is, but the easiest way I can think of making a thimble with a hole in the top is by making a mould like I have done. Since the centre of the thimble has to be there to ensure it is a ring of metal, it seemed easiest to have a piece of clay running through that point.
Earlier thimble with hole in top (14th C or so):
Eraly medieval thimble
Later medieval thimble, more like today’s (15th century):
Later medieval thimble
My moulds:
The first mould
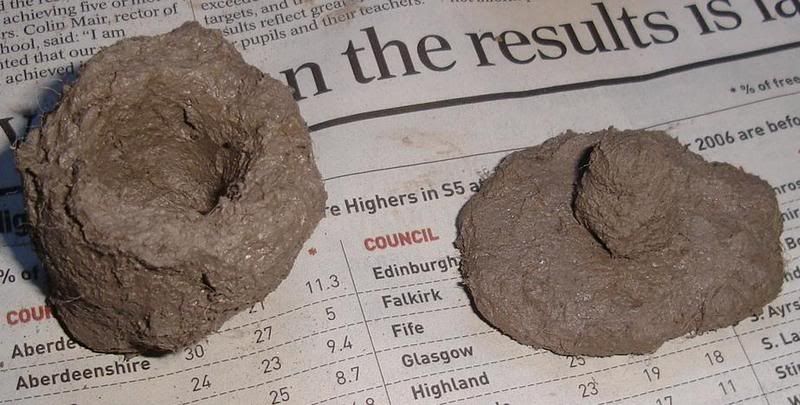
The second mould:
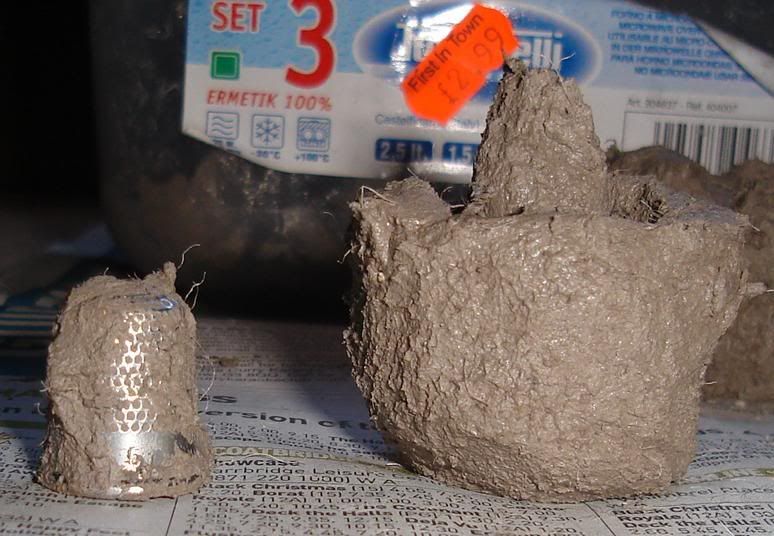
There is a thimble beside it for comparison.
Now, I dried these moulds in a warm but not hot oven for an hour or two, then ramped up the temperature to over 100C for an hour. They were then fired to something towards 600C in this set up:
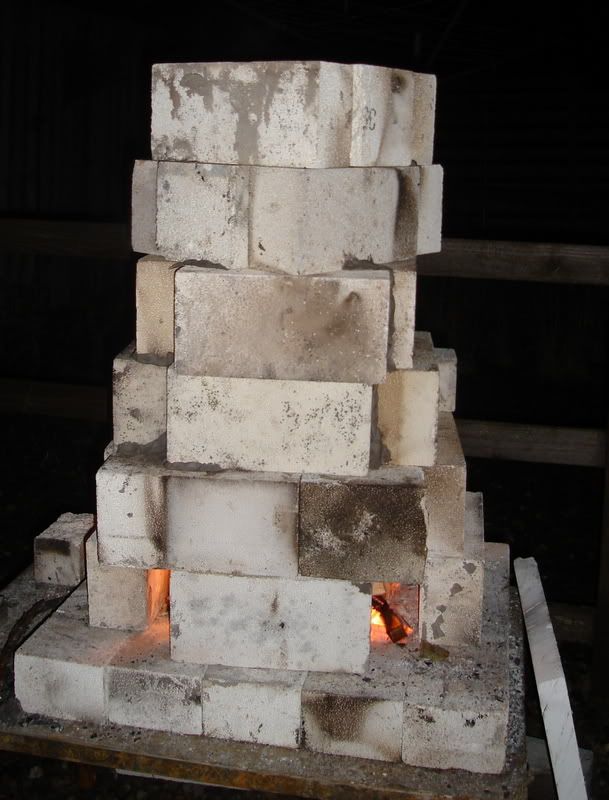
I was experimenting with chimneys, so built it high. The gaps at the side had some clay on them, to seal it off a bit better to ensure that it worked as chimney. Maybe I made it close in too much at the top, but it didn’t work quite as well as last time. Part of the problem was that I was using wood that wasn’t quite dry enough, and was quite green. So it didn’t take off too well. But the thermocouple registered just over 800C in the embers when it was going properly. For the chimney effect to work properly I need a good lot of heat at the bottom, to heat air and provide combustion gases, thus pulling more air in at the bottom. You end up with lots of air getting to the fire for no other reason than the fire itself. From the description of a similar set up in Theophilus, mine was not good enough, it should be able to reach a temperature of over 900, which is what is needed for making brass.
They came out fine, looking like this:
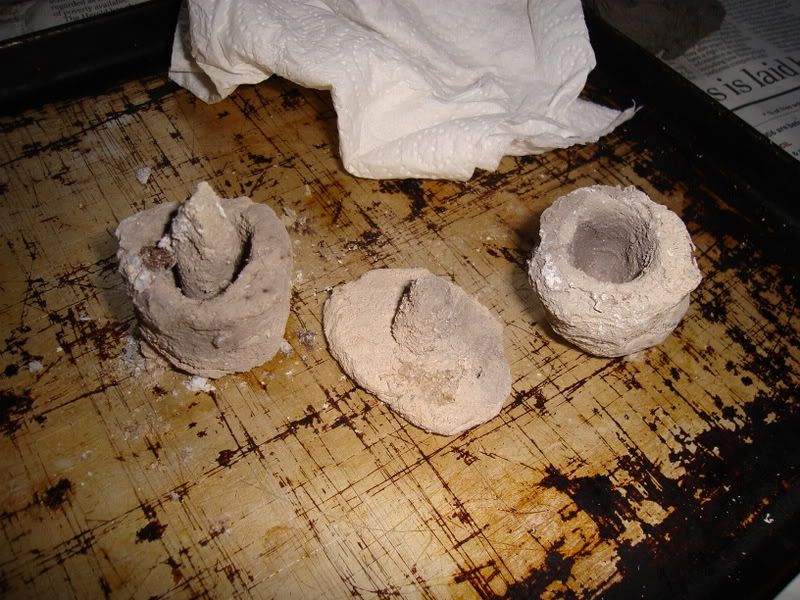
No cracking apparent. I shall still put them in the furnace at over 1000 when I’m melting the copper, just to make sure that they are properly fired.
After I’d made my clay moulds, I found a comment in the journal of the Historical metallurgy society, 30/2, 1996, page 112, saying that the mould material they had found on an archeological dig was clay tempered by organic matter. Yes, great, but what kind of organic matter? I shall probably have to try leaves, potting compost, and plain old earth.
It is likely that there are some people out there doing this using nearly authentic techniques, but half the fun of this is working it out for myself, and at the end I shall have a much better idea of what makes things work well when doing historical metallurgy.
Update on my Spanish Green experiment- after 2 days, the copper in the vinegar solution has not turned green, but the copper above it has done so. This suggests that the main reason it will turn green is reaction with acetic acid vapour. Copper acetate being the result. So for larger scale production, it shall be necessary to merely heat vinegar gently, with copper suspended above it. Why didn’t they use this method then?
Making moulds out of clay for objects is annoyingly poorly described. No doubt each master had his own specific recipes; these would probably vary by geography given the availability of local ingredients. Biringuccio, in his “Pirotechnia”, from 1540, is quite specific about all this. He says:
“There are many kinds and varieties of earth that are used for the loam compositions for making the moulds for casting bronze, brass, or other metals. Since this is a very necessary thing, you must try to have the best kind and one that resists the fire well. It must be disposed to receive the metals well, must make a neat casting, and must not shrink or break with cracks on drying or baking. Aside from actual trial, I believe that there is little that can help you, since the clay in itself has no colour or visible sign that I know of to show how satisfactory it is.”
Or in other words, whether it is red, or yellow, or brown, it is not clear as to exactly what kind of clay you should use, but the final product will be obviously good or bad. Difficulties of knowing exactly what to use are compounded by the fact that there is a translators note at the bottom of the page:
“Terra this word was used for earthy materials in general as well as specifically for clay such as used in moulding. We have used either earth or clay as seemed best fitted to the context.”
Or in other words, is Biringuccio talking about earth with much organic material in it, or just for clay? How much sand is in it? Further on he talks about using wool cloth clippings, wool cardings, and sand, iron scale, crushed brick, horse or donkey dung and a variety of other materials. All of these would add some strength to the clay, assuming we are talking about pure clay here. This pure clay would have to be smooth and lacking in lumps and bits of stone, in order to avoid voids and weak spots in the mould. This is easy for me to get nowadays, but much harder for people in the past. Also Biringuccio says it should not be unctuous or lean, characteristics that are somewhat unclear in the context of a book. Perhaps with samples in front of me they would make perfect sense. Also, he appears not to like the use of pure clay, saying “In conclusions, with the exception of pure clay (which is too viscous and tenacious), any other earth, if free from pebbles, could easily serve you by tempering it with others, or if it should have pebbles, by separating them out.”
Biringuccio was greatly enamoured of wool clippings for helping the clay stay good and strong. They would act like a composite, giving greater strength through having these small fibres running through the clay. But there is nothing about how long they would be. I suspect they would be a few mm, but it is not clear. So I shall have to experiment.
I cut up some wool I gathered from fences and ended up with fibres 2 or 3mm long. Together with fine grained sand from the local sandpit, and and buff clay, with a bit of charcoal and some of the strange ashes you get from charcoal briquettes. (Charcoal briquettes are rubbish for my purposes, since they do not burn fast enough.) I have no idea if anything is special about buff clay, but it seems to work, and some googling suggests it is good for modelling etc.
Clay is sticky stuff when wet. I had trouble getting it to stop sticking to my fingers, next time I shall use much dryer clay. Again, from the old books it is not clear how wet it should be. I managed to make two kinds of mould for thimbles. The first, is made of two parts. The aim was to have a top, with a lump sticking down from it to fill in the hollow in the bottom part. This kind of worked, but I forgot to put in the pouring holes so shall have to drill them out. The second kind was made of a hollow, with a lump placed into the middle of it. The aim was to mimic medieval thimbles. The earlier kind, that the second mould is made for, had a hole in the top. Now, I have yet to find any mention of why this is, but the easiest way I can think of making a thimble with a hole in the top is by making a mould like I have done. Since the centre of the thimble has to be there to ensure it is a ring of metal, it seemed easiest to have a piece of clay running through that point.
Earlier thimble with hole in top (14th C or so):
Eraly medieval thimble
Later medieval thimble, more like today’s (15th century):
Later medieval thimble
My moulds:
The first mould
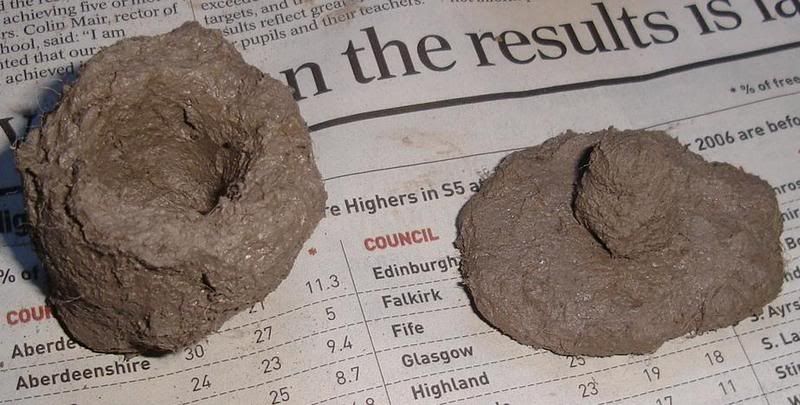
The second mould:
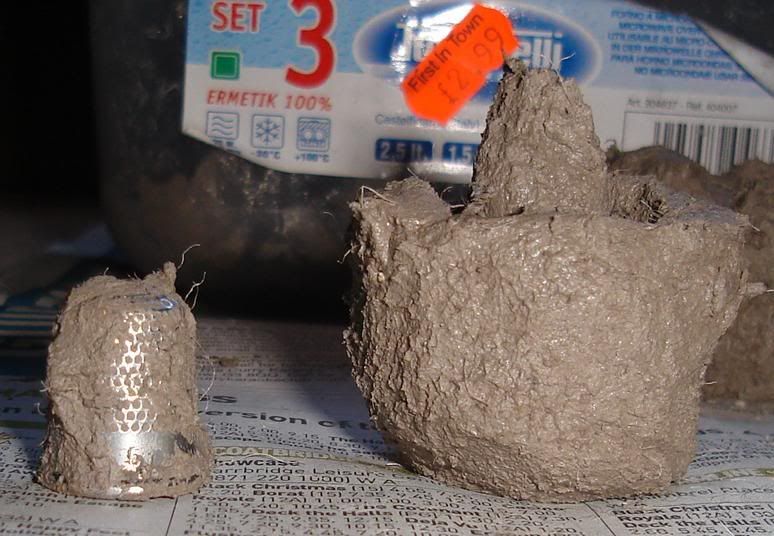
There is a thimble beside it for comparison.
Now, I dried these moulds in a warm but not hot oven for an hour or two, then ramped up the temperature to over 100C for an hour. They were then fired to something towards 600C in this set up:
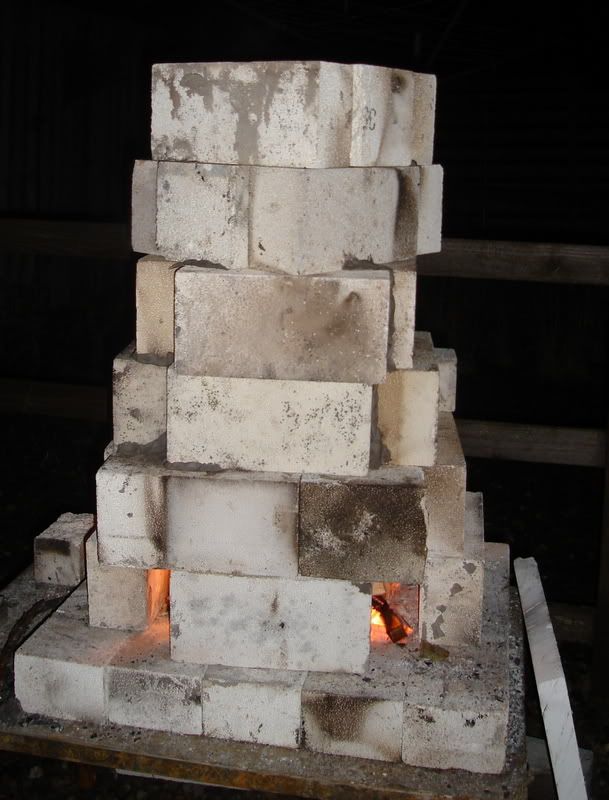
I was experimenting with chimneys, so built it high. The gaps at the side had some clay on them, to seal it off a bit better to ensure that it worked as chimney. Maybe I made it close in too much at the top, but it didn’t work quite as well as last time. Part of the problem was that I was using wood that wasn’t quite dry enough, and was quite green. So it didn’t take off too well. But the thermocouple registered just over 800C in the embers when it was going properly. For the chimney effect to work properly I need a good lot of heat at the bottom, to heat air and provide combustion gases, thus pulling more air in at the bottom. You end up with lots of air getting to the fire for no other reason than the fire itself. From the description of a similar set up in Theophilus, mine was not good enough, it should be able to reach a temperature of over 900, which is what is needed for making brass.
They came out fine, looking like this:
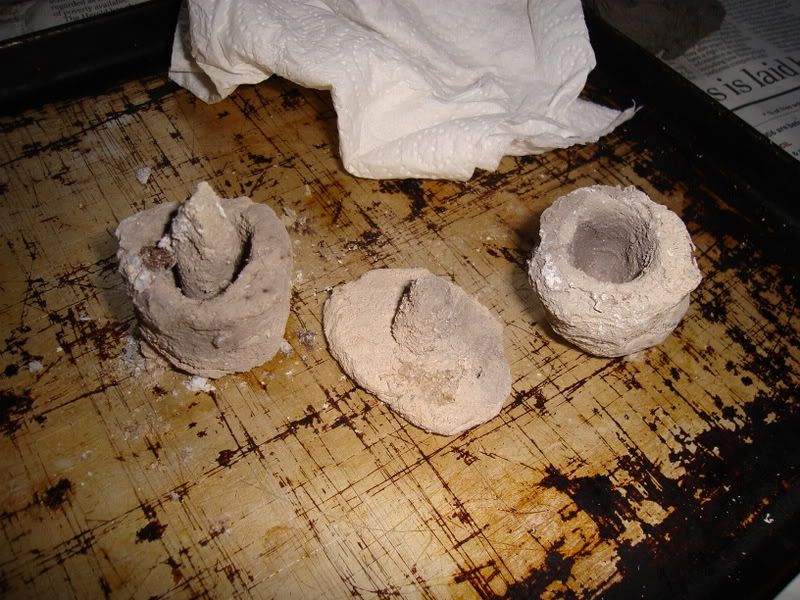
No cracking apparent. I shall still put them in the furnace at over 1000 when I’m melting the copper, just to make sure that they are properly fired.
After I’d made my clay moulds, I found a comment in the journal of the Historical metallurgy society, 30/2, 1996, page 112, saying that the mould material they had found on an archeological dig was clay tempered by organic matter. Yes, great, but what kind of organic matter? I shall probably have to try leaves, potting compost, and plain old earth.
It is likely that there are some people out there doing this using nearly authentic techniques, but half the fun of this is working it out for myself, and at the end I shall have a much better idea of what makes things work well when doing historical metallurgy.
Update on my Spanish Green experiment- after 2 days, the copper in the vinegar solution has not turned green, but the copper above it has done so. This suggests that the main reason it will turn green is reaction with acetic acid vapour. Copper acetate being the result. So for larger scale production, it shall be necessary to merely heat vinegar gently, with copper suspended above it. Why didn’t they use this method then?
Wednesday, January 31, 2007
Intelligent Design Creationism
[Warming- rant involving swear words and unpleasantness. This is my blog and I am allowed to let off steam here.]
The latest Creationist attack in the UK is a group called “Truth in Science”. Personally I call them “Truthiness in science”. ( http://en.wikipedia.org/wiki/Truthiness )
They would make Goebbels or Karl Rove proud, in their carefully plotted campaign against Evolution. They have sent out a bunch of DVDs and lesson plans to every secondary school in the country, suggesting that they be used to show the alternatives to “Darwinism”. Now, the alternative to Darwinism is Evolutionary Biology, but they don’t want you to know that.* Instead, in the lesson plans on their website, they push several Intelligent Designs arguments, such as irreducible complexity. The really ironic thing is that Truth in science are actually Young Earth Creationists!
The cheek is amazing- instead of honestly saying “We’re Creationists, we think God takes precedence over science”, they are actually now saying “Here’s some scientific reasons why evolution is wrong”, but not mentioning God at all.
Needless to say, “Truth in Science” also bring in the peppered moth as a problem with Evolution. In fact every so called argument on their website is either a mischaracterization or involves question begging. Their website argues about teaching alternatives to Evolution, yet they persistently do not state what such alternative is on their website! Just go and read it. Nowhere do they say “Our Christian God did it”. I am sure that most true Christians would be horrified by the way that this group hides their antecedents and aims. I too am horrified, agnostic though I am. I hate it when people are mendacious and try and cover things up.
They even say:
Yes, a significant minority of qualified scientists do not believe that Darwinian evolution can explain the origin of the diversity of life we see around us. For example, over 600 scientists with PhDs have signed a public statement: "We are skeptical of claims for the ability of random mutation and natural selection to account for the complexity of life. Careful examination of the evidence for Darwinian theory should be encouraged.”
(From: http://www.truthinscience.org.uk/site/content/view/109/54/)
They bring up the very old public statement. Project Steve was started by “darwinists” who only wanted people with Biology qualifications called Steve or Steven etc to sign up to it. They have more people signed up to it than the Creationists have!
It is however typical of their reliance upon appeals to authority. All their press releases make much out of the fact that some of their supporters are university professors. Oddly enough none of these professors have published scientific papers showing that “Darwinism” is wrong, nevertheless they insist on claiming so.
Another sign of their antecedents and desire to cover their tracks is this essay:
http://www.truthinscience.org.uk/site/content/view/55/65/
by Paul Garner, on the evolution of the horse. If you google on his name and “horse”, you find this essay:
http://www.biblicalcreation.org.uk/scientific_issues/bcs146.html
They are functionally identical. The first one, on the TiS website has merely had some of the pictures and more complex stuff removed, and more importantly, had all reference to a flood elided.
Yes, the Creationists are trying to show that they are not creationists, by re-modelling an essay. A fuller explanation can be found here:
http://www.justscience.org.uk/tikiwiki-1.9.5/tiki-read_article.php?articleId=14
It is classic lying by omission. The essay even ends by saying that actually the sequence of horse fossils is neutral as to whether evolution or creationism is correct. Which is a lie. In science, you have to look at the big picture. In this case, everything from the age of the earth through to molecular genetics shows that the horse sequence of fossils is a really good example of evolution in action.
Now, part of the public relations problem that those of us who support real science face, is that a weak form of intelligent design is the default position for many people. After all, who set the universe in motion? Obviously [insert deity of choice] did, since it must have started somehow. Sure, I have no problem with this position in general. But claiming that there is scientific evidence to support it is utterly wrong. We have yet to scientifically prove the existence of [insert deity of choice]. Remember that it is also impossible to prove the non-existence of [insert deity of choice] because we do not know everything about the universe- it’s the infamous you can’t prove a negative problem.
-----
This of course does not stop TiS. They spew propaganda all over the place. Take this post for example (my comments are in bold):
http://www.truthinscience.org.uk/site/content/view/217/63/
As reported yesterday in the Sunday Times, twelve senior academics have written to the Prime Minister and Education Secretary in support of Truth in Science.
The group was led by Norman Nevin OBE, Professor Emeritus of Medical Genetics, Queen's University of Belfast and included Antony Flew, former Professor of Philosophy at Reading University and a distinguished supporter of humanism.
Look at our big names! Never mind that Flew has converted to some form of deism, although he is very coy about what kind. Nor that Nevin is also religiously motivated, as can be found out by anyone with internet access.
"We write to applaud the Truth in Science initiative," the letter said. Empirical science has to recognise "severe limitations concerning origins" and Darwinism is not necessarily "the best scientific model to fit the data that we observe".
What limitations on empirical science, you fuckwits? It’s the only kind of science there is. The reader will note that at no time do they actually say what this non empirical science actually involves. This is typical creationist fertiliser. But they are right about one thing. Darwinism is not the best scientific model to fit the data. The actual best fit comes from modern evolutionary biology.
They concluded: "We ask therefore that, where schools so choose, you ensure an open and honest approach to this subject under the National Curriculum, at the same time ensuring that the necessary criteria are maintained to deliver a rigorous education."
An honest approach would involve the teacher leading an hour long lesson on the differences between pseudoscience and real science, with creationism firmly in the former camp.
The other signatories were: David Back, Professor of Pharmacology at the University of Liverpool; Steve Fuller, Professor of Sociology at Warwick University; Mart de Groot, Director, Retired, Armagh Astronomical Observatory; Terry Hamblin, Professor of Immunohaematology, University of Southampton; Colin Reeves, Professor of Operational Research at Coventry University and John Walton, Professor of Chemistry, St Andrews University, as well as the three University Professors who are members of the TiS Board and Council.
John Walton is a 7th day adventist from my old university. Steve Fuller is some kind of make believe philosopher who thinks that the reigning paradigm should always be challenged, and therefore non science like ID should be supported. He appears to be the only one here without a religious agenda.
Professor Norman Nevin has authored over 300 peer-reviewed publications on various aspects of genetics, especially single gene disorders and congenital abnormalities. In his distinguished career he has held the posts: Head of the Northern Regional Genetics Service, President of the UK Clinical Genetics Society, member of the Human Genetics Advisory Commission and of the subsequent Human Genetics Commission, member of the European Concerted Action for Congenital Abnormalities, Chairman of the UK Gene Therapy Advisory Committee (GTAC). In 2003 he received an OBE for his services to gene therapy.
Look at our qualifications, now, do you believe everything we say? Obviously someone who has had such a productive professional life can’t be wrong?
On 11 December, Professor Nevin received a response from the Department for Education and Skills' Public Communications Unit on behalf of both the Prime Minster and the Education Secretary. The support for Truth in Science had been "noted by the Department" but the "vast majority" of enquiries that the DfES received had "expressed concern" about the Truth in Science resource pack.
Yes. Most of the replies would have said “Fuck off and die, Creationist scum”, except that MP’s don’t really like reading that kind of letter, so they were toned down.
"Intelligent design is not a recognised scientific theory" the Department claimed "and is therefore not included in the science curriculum. The Truth in Science information pack is not therefore an appropriate resource to support the science curriculum."
Spot on!
However, intelligent design could discussed in science classes in response to pupil's questions: "During a science lesson on evolution it is possible that pupils may ask about creationism and intelligent design. In this situation, the Department would expect teachers to answer pupil's questions about this and other beliefs in a balanced way."
Yes. Here’s a scientific balance. On this side, I’ll put 3kg of lead. On the other side I’ll put this nitrogen molecule. Guess which is evolutionary biology?
----
TiS are operating with a sophisticated but non-mainstream propaganda machine. This limits their activities somewhat. Since they are so religiously based, it is very hard for them to break out of the fundamentalist churches they thrive in.
A sign of this is the effort that senior TiS people are having to put in on the propaganda front. For example, Richard Buggs, one of their “scientific” (scare quotes deliberate) advisors, had an article in the guardian:
http://www.guardian.co.uk/comment/story/0,,1985698,00.html
It is simple creationist boilerplate. Astounding in its mendacity and sleight of mind. For example, he says:
“If Darwin had known what we now know about molecular biology - gigabytes of coded information in DNA, cells rife with tiny machines, the highly specific structures of certain proteins - would he have found his own theory convincing? Randerson thinks that natural selection works fine to explain the origin of molecular machines. But the fact is that we are still unable even to guess Darwinian pathways for the origin of most complex biological structures.”
Rubbish! If Darwin had known about the nested hierarchies, the way we can trace mutations through species, the “molecular clocks”, the basic similarities between all species on the planet, he would have heaved a huge sigh of relief, since it would have filled in many of the gaps and uncertainties in his theory. After all, Bugg’s supposed argument is simply a restatement of the idea that since a birds wings operate so well to help it fly, it must have been designed by a deity. It is a simple argument from incredulosity, and indicates the limited mindsets of the intellectual pygmies that are Creationists.
We have multiple possible pathways for the evolution of bits of the immune system, and many more ideas about the evolution of a host of other cellular functions. (http://www.talkorigins.org/indexcc/CB/CB200_4.html)
The more astute amongst you will recognize that Buggs spends a fair bit of time in his article trying to say that since “Darwinism” can’t explain everything, there must be another answer that is correct. Yet he never comes out with it. What kind of Christian refuses to give the real reason for his opposition to something?
I am pleased to note that the article got the same kind of reception that HG Well’s Martians would if they invaded us today. I was in there, commenting like mad, it was fun.
One last LIE from Richard Buggs Guardian article:
“In fact, ID is a logical inference, based on data gathered from the natural world, and hence it is firmly in the realm of science. It does not rely upon the Bible, the Qur'an, or any religious authority or tradition - only on scientific evidence.”
No other word will do, except the word lie. Firstly, logical inferences are not science, they have to be tested. The ID pushers have not tested any of their inferences. Dembski has signally failed to produce any calculations using his probability maths. Behe is unable to offer anything except an ability to ignore the evidence, as shown at the Dover trial in the USA, where an attempt to get ID into schools failed the Lemon test, and ID was also branded religiously inspired to boot.
More on the Dover trial:
http://www.pandasthumb.org/archives/2005/12/waterloo_in_dov.html
The outcome of this trial was that intelligent design was legally found to be religiously inspired, and not based in science. TiS have no mention of this trial on their website at all. Can anyone else say lying bastards?
One of the bigwigs in TiS is Professor Andy McIntosh, of Leeds university. He is fond of making statements such as (taken from the TiS website:
The principles of thermodynamics even in open systems do not allow a new function using raised free energy levels to be achieved without new machinery. And new machines are not made by simply adding energy to existing machines.
And this thesis is falsifiable. If anyone was to take an existing chemical machine and produce a different chemical machine which was not there before (either as a sub-part or latently coded for in the DNA template) then this argument would have been falsified.
Stop and think about this for a minute. What exactly has free energy (G, Gibbs free energy) got to do with machinery? You will note that he does not provide any supportive references for his claim. Moreover, the second section is laughable. New structures are often formed when bacteria develop antibiotic resistance, or when they learn to digest nylon. Or in the case of sickle cell anemia, when a gene or two mutate, with the end result of making your red blood cells sickle shaped.
He appeared on the radio twice, talking about his amazing insight into evolutionary biology that he hadn’t actually bothered to try and publish anywhere. The link below takes you to an attempt by him to clarify his position:
http://www.bbc.co.uk/blogs/ni/2007/01/the_thermodynamics_of_andy_mci.html
This is what he said, my comments in SHOUTY:
Thermodynamics as I have explained before, does lie at the heart of the debate. Boeing 777s cannot be made in a car factory unless the machinery is available to do so
BUT THEY ARE MADE USING SMALLER MACHINES TO MAKE BITS OF THE LARGER ONE, ARE THEY NOT? BESIDES, WHEN DID YOU LAST SEE A PAIR OF MATING 777’S?
Similarly the human brain cannot be formed from simpler machines if there is no machinery available to do this.
THEY’RE CALLED CELLS, YOU MORON.
Spontaneously forming such will not happen, even with natural selective forces at work
AND YOU KNOW THIS HOW? BESIDES, NOBODY IS SAYING THAT CELLS AS THEY ARE TODAY SPRANG SPONTANEOUSLY INTO BEING.
All natural selection will do is select from what is there already.
INDEED.
It will not create a new machine which was not there before (either as a sub-machine or coded in embryonic form).
NO, YOU MICROCEPHALIC PINHEAD. MUTATION IS WHAT YOU ARE LOOKING FOR THERE, NOT NATURAL SELECTION. HERE YOU CAN SEE HIS IGNORANCE OF BIOLOGY.
An open thermodynamic system is not the answer either since simply adding energy to existing machinery will not change what is there already to a new machine.
BUT WHAT IF THE MACHINERY IN QUESTION CAN BE REFORMED, LIKE OUR DNA IS? LOOK AT MUTATIONS- THEY CAUSE CHANGES IN THE MACHINE THAT FORMS OUR PROTEINS ETC ETC. IN FACT, I SUGGEST THAT MUTATIONS MAY WELL BE THERMODYNAMICALLY FAVOURED, SINCE WE ARE DEALING WITH THE ATOMIC LEVEL, WHERE THINGS CAN CHANGE WITHOUT ANY DEFINITE INPUT.
To quote Wilder Smith whose book 'The natural sciences know nothing of evolution' is available on the web - p. 146 "Today it is simply unscientific to claim that the fantastically reduced entropy of the human brain, of the dolphin's sound lens, and of the eye of a fossilised trilobite simply "happened", for experimental experience has shown that such miracles just do not "happen"."
MORE QUOTING, NO EVIDENCE. WHAT IS THIS SIMPLY HAPPENED THING? DO THEY THINK THAT THEY DROPPED OUT OF THE SKY ONE DAY? NOT TO MENTION THE HUGE AMOUNT OF EVIDENCE SHOWING THAT THEY CAN EVOLVE ANYWAY.
My position is to side with experimental science and not with 'just so' attempts to get round the clear evidence of design in nature. At the very least these matters should be critically considered in science teaching today.
WHAT EXPERIMENTAL SCIENCE, YOU MORON? CREATIONISTS, NAY, CRETINISTS LIKE YOURSELF HAVE NOT DONE ANY. WHERE ARE THE DETAILED THERMODYNAMIC CALCULATIONS SHOWING THAT YOUR STATEMENTS ABOUT FREE NERGY LEVELS IN CELLS ETC ARE CORRECT? A MAN OF YOUR EDUCATION CAN SURELY PERFORM SUCH CALCULATIONS, AND DAZZLE US ALL WITH YOUR GRASP OF SCIENCE!
I don’t think we’ll see anything from Mcintosh about his scientific basis for his belief. Suffice to say, he is a laughing stock.
Ultimately, the most laughable thing about it is that the Creationists come across as arch materialists, with their insistence on machinery in cells.
Other entertainment can be had here:
http://idintheuk.blogspot.com/
http://www.exilefromgroggs.blogspot.com/
Meanwhile, on the BBC blog here:
http://www.bbc.co.uk/blogs/ni/
I have run into such a monumentally stupid poster that even I have trouble believing it. They insist on conflating methodological naturalism, which is what science does, considering only things which are material, that can be sensed etc, with philosophical naturalism, which says that there are only natural things in the universe, that there are no supernatural entities. So he claims that science is atheistic, because it says nothing about god, indeed can only work when you disregard supernatural entities.
Well, duh.
Science only looks at material things. It has nothing to say about gods.
So, if you are concerned about TiS and their stupidity, please write to your MP expressing your concern.
* Evolutionary science has undergone at least 2 revisions since Darwin’s time. These have integrated what we now know of genetics and other influences upon evolution into the science of Evolutionary Biology. More information here:
http://www.talkorigins.org/faqs/modern-synthesis.html
It is worth reminding people that Creationists will quote mine sentences from scientific sources that appear to damage Evolutionary theory, whilst ignoring that the source as a whole actually backs evolution. It is quote common for scientists to say something like “This blows a huge hole in the current way of thinking about this.” (They are human after all and like hyperbola just like the rest of us, not to mention puffing themselves up) The Creationists then quote this sentence, whilst ignoring that the next sentence says “Fortunately, my work shows that if you integrate this, this and that, because of X, then actually its no problem at all and it all fits nicely within Evolution”.
The latest Creationist attack in the UK is a group called “Truth in Science”. Personally I call them “Truthiness in science”. ( http://en.wikipedia.org/wiki/Truthiness )
They would make Goebbels or Karl Rove proud, in their carefully plotted campaign against Evolution. They have sent out a bunch of DVDs and lesson plans to every secondary school in the country, suggesting that they be used to show the alternatives to “Darwinism”. Now, the alternative to Darwinism is Evolutionary Biology, but they don’t want you to know that.* Instead, in the lesson plans on their website, they push several Intelligent Designs arguments, such as irreducible complexity. The really ironic thing is that Truth in science are actually Young Earth Creationists!
The cheek is amazing- instead of honestly saying “We’re Creationists, we think God takes precedence over science”, they are actually now saying “Here’s some scientific reasons why evolution is wrong”, but not mentioning God at all.
Needless to say, “Truth in Science” also bring in the peppered moth as a problem with Evolution. In fact every so called argument on their website is either a mischaracterization or involves question begging. Their website argues about teaching alternatives to Evolution, yet they persistently do not state what such alternative is on their website! Just go and read it. Nowhere do they say “Our Christian God did it”. I am sure that most true Christians would be horrified by the way that this group hides their antecedents and aims. I too am horrified, agnostic though I am. I hate it when people are mendacious and try and cover things up.
They even say:
Yes, a significant minority of qualified scientists do not believe that Darwinian evolution can explain the origin of the diversity of life we see around us. For example, over 600 scientists with PhDs have signed a public statement: "We are skeptical of claims for the ability of random mutation and natural selection to account for the complexity of life. Careful examination of the evidence for Darwinian theory should be encouraged.”
(From: http://www.truthinscience.org.uk/site/content/view/109/54/)
They bring up the very old public statement. Project Steve was started by “darwinists” who only wanted people with Biology qualifications called Steve or Steven etc to sign up to it. They have more people signed up to it than the Creationists have!
It is however typical of their reliance upon appeals to authority. All their press releases make much out of the fact that some of their supporters are university professors. Oddly enough none of these professors have published scientific papers showing that “Darwinism” is wrong, nevertheless they insist on claiming so.
Another sign of their antecedents and desire to cover their tracks is this essay:
http://www.truthinscience.org.uk/site/content/view/55/65/
by Paul Garner, on the evolution of the horse. If you google on his name and “horse”, you find this essay:
http://www.biblicalcreation.org.uk/scientific_issues/bcs146.html
They are functionally identical. The first one, on the TiS website has merely had some of the pictures and more complex stuff removed, and more importantly, had all reference to a flood elided.
Yes, the Creationists are trying to show that they are not creationists, by re-modelling an essay. A fuller explanation can be found here:
http://www.justscience.org.uk/tikiwiki-1.9.5/tiki-read_article.php?articleId=14
It is classic lying by omission. The essay even ends by saying that actually the sequence of horse fossils is neutral as to whether evolution or creationism is correct. Which is a lie. In science, you have to look at the big picture. In this case, everything from the age of the earth through to molecular genetics shows that the horse sequence of fossils is a really good example of evolution in action.
Now, part of the public relations problem that those of us who support real science face, is that a weak form of intelligent design is the default position for many people. After all, who set the universe in motion? Obviously [insert deity of choice] did, since it must have started somehow. Sure, I have no problem with this position in general. But claiming that there is scientific evidence to support it is utterly wrong. We have yet to scientifically prove the existence of [insert deity of choice]. Remember that it is also impossible to prove the non-existence of [insert deity of choice] because we do not know everything about the universe- it’s the infamous you can’t prove a negative problem.
-----
This of course does not stop TiS. They spew propaganda all over the place. Take this post for example (my comments are in bold):
http://www.truthinscience.org.uk/site/content/view/217/63/
As reported yesterday in the Sunday Times, twelve senior academics have written to the Prime Minister and Education Secretary in support of Truth in Science.
The group was led by Norman Nevin OBE, Professor Emeritus of Medical Genetics, Queen's University of Belfast and included Antony Flew, former Professor of Philosophy at Reading University and a distinguished supporter of humanism.
Look at our big names! Never mind that Flew has converted to some form of deism, although he is very coy about what kind. Nor that Nevin is also religiously motivated, as can be found out by anyone with internet access.
"We write to applaud the Truth in Science initiative," the letter said. Empirical science has to recognise "severe limitations concerning origins" and Darwinism is not necessarily "the best scientific model to fit the data that we observe".
What limitations on empirical science, you fuckwits? It’s the only kind of science there is. The reader will note that at no time do they actually say what this non empirical science actually involves. This is typical creationist fertiliser. But they are right about one thing. Darwinism is not the best scientific model to fit the data. The actual best fit comes from modern evolutionary biology.
They concluded: "We ask therefore that, where schools so choose, you ensure an open and honest approach to this subject under the National Curriculum, at the same time ensuring that the necessary criteria are maintained to deliver a rigorous education."
An honest approach would involve the teacher leading an hour long lesson on the differences between pseudoscience and real science, with creationism firmly in the former camp.
The other signatories were: David Back, Professor of Pharmacology at the University of Liverpool; Steve Fuller, Professor of Sociology at Warwick University; Mart de Groot, Director, Retired, Armagh Astronomical Observatory; Terry Hamblin, Professor of Immunohaematology, University of Southampton; Colin Reeves, Professor of Operational Research at Coventry University and John Walton, Professor of Chemistry, St Andrews University, as well as the three University Professors who are members of the TiS Board and Council.
John Walton is a 7th day adventist from my old university. Steve Fuller is some kind of make believe philosopher who thinks that the reigning paradigm should always be challenged, and therefore non science like ID should be supported. He appears to be the only one here without a religious agenda.
Professor Norman Nevin has authored over 300 peer-reviewed publications on various aspects of genetics, especially single gene disorders and congenital abnormalities. In his distinguished career he has held the posts: Head of the Northern Regional Genetics Service, President of the UK Clinical Genetics Society, member of the Human Genetics Advisory Commission and of the subsequent Human Genetics Commission, member of the European Concerted Action for Congenital Abnormalities, Chairman of the UK Gene Therapy Advisory Committee (GTAC). In 2003 he received an OBE for his services to gene therapy.
Look at our qualifications, now, do you believe everything we say? Obviously someone who has had such a productive professional life can’t be wrong?
On 11 December, Professor Nevin received a response from the Department for Education and Skills' Public Communications Unit on behalf of both the Prime Minster and the Education Secretary. The support for Truth in Science had been "noted by the Department" but the "vast majority" of enquiries that the DfES received had "expressed concern" about the Truth in Science resource pack.
Yes. Most of the replies would have said “Fuck off and die, Creationist scum”, except that MP’s don’t really like reading that kind of letter, so they were toned down.
"Intelligent design is not a recognised scientific theory" the Department claimed "and is therefore not included in the science curriculum. The Truth in Science information pack is not therefore an appropriate resource to support the science curriculum."
Spot on!
However, intelligent design could discussed in science classes in response to pupil's questions: "During a science lesson on evolution it is possible that pupils may ask about creationism and intelligent design. In this situation, the Department would expect teachers to answer pupil's questions about this and other beliefs in a balanced way."
Yes. Here’s a scientific balance. On this side, I’ll put 3kg of lead. On the other side I’ll put this nitrogen molecule. Guess which is evolutionary biology?
----
TiS are operating with a sophisticated but non-mainstream propaganda machine. This limits their activities somewhat. Since they are so religiously based, it is very hard for them to break out of the fundamentalist churches they thrive in.
A sign of this is the effort that senior TiS people are having to put in on the propaganda front. For example, Richard Buggs, one of their “scientific” (scare quotes deliberate) advisors, had an article in the guardian:
http://www.guardian.co.uk/comment/story/0,,1985698,00.html
It is simple creationist boilerplate. Astounding in its mendacity and sleight of mind. For example, he says:
“If Darwin had known what we now know about molecular biology - gigabytes of coded information in DNA, cells rife with tiny machines, the highly specific structures of certain proteins - would he have found his own theory convincing? Randerson thinks that natural selection works fine to explain the origin of molecular machines. But the fact is that we are still unable even to guess Darwinian pathways for the origin of most complex biological structures.”
Rubbish! If Darwin had known about the nested hierarchies, the way we can trace mutations through species, the “molecular clocks”, the basic similarities between all species on the planet, he would have heaved a huge sigh of relief, since it would have filled in many of the gaps and uncertainties in his theory. After all, Bugg’s supposed argument is simply a restatement of the idea that since a birds wings operate so well to help it fly, it must have been designed by a deity. It is a simple argument from incredulosity, and indicates the limited mindsets of the intellectual pygmies that are Creationists.
We have multiple possible pathways for the evolution of bits of the immune system, and many more ideas about the evolution of a host of other cellular functions. (http://www.talkorigins.org/indexcc/CB/CB200_4.html)
The more astute amongst you will recognize that Buggs spends a fair bit of time in his article trying to say that since “Darwinism” can’t explain everything, there must be another answer that is correct. Yet he never comes out with it. What kind of Christian refuses to give the real reason for his opposition to something?
I am pleased to note that the article got the same kind of reception that HG Well’s Martians would if they invaded us today. I was in there, commenting like mad, it was fun.
One last LIE from Richard Buggs Guardian article:
“In fact, ID is a logical inference, based on data gathered from the natural world, and hence it is firmly in the realm of science. It does not rely upon the Bible, the Qur'an, or any religious authority or tradition - only on scientific evidence.”
No other word will do, except the word lie. Firstly, logical inferences are not science, they have to be tested. The ID pushers have not tested any of their inferences. Dembski has signally failed to produce any calculations using his probability maths. Behe is unable to offer anything except an ability to ignore the evidence, as shown at the Dover trial in the USA, where an attempt to get ID into schools failed the Lemon test, and ID was also branded religiously inspired to boot.
More on the Dover trial:
http://www.pandasthumb.org/archives/2005/12/waterloo_in_dov.html
The outcome of this trial was that intelligent design was legally found to be religiously inspired, and not based in science. TiS have no mention of this trial on their website at all. Can anyone else say lying bastards?
One of the bigwigs in TiS is Professor Andy McIntosh, of Leeds university. He is fond of making statements such as (taken from the TiS website:
The principles of thermodynamics even in open systems do not allow a new function using raised free energy levels to be achieved without new machinery. And new machines are not made by simply adding energy to existing machines.
And this thesis is falsifiable. If anyone was to take an existing chemical machine and produce a different chemical machine which was not there before (either as a sub-part or latently coded for in the DNA template) then this argument would have been falsified.
Stop and think about this for a minute. What exactly has free energy (G, Gibbs free energy) got to do with machinery? You will note that he does not provide any supportive references for his claim. Moreover, the second section is laughable. New structures are often formed when bacteria develop antibiotic resistance, or when they learn to digest nylon. Or in the case of sickle cell anemia, when a gene or two mutate, with the end result of making your red blood cells sickle shaped.
He appeared on the radio twice, talking about his amazing insight into evolutionary biology that he hadn’t actually bothered to try and publish anywhere. The link below takes you to an attempt by him to clarify his position:
http://www.bbc.co.uk/blogs/ni/2007/01/the_thermodynamics_of_andy_mci.html
This is what he said, my comments in SHOUTY:
Thermodynamics as I have explained before, does lie at the heart of the debate. Boeing 777s cannot be made in a car factory unless the machinery is available to do so
BUT THEY ARE MADE USING SMALLER MACHINES TO MAKE BITS OF THE LARGER ONE, ARE THEY NOT? BESIDES, WHEN DID YOU LAST SEE A PAIR OF MATING 777’S?
Similarly the human brain cannot be formed from simpler machines if there is no machinery available to do this.
THEY’RE CALLED CELLS, YOU MORON.
Spontaneously forming such will not happen, even with natural selective forces at work
AND YOU KNOW THIS HOW? BESIDES, NOBODY IS SAYING THAT CELLS AS THEY ARE TODAY SPRANG SPONTANEOUSLY INTO BEING.
All natural selection will do is select from what is there already.
INDEED.
It will not create a new machine which was not there before (either as a sub-machine or coded in embryonic form).
NO, YOU MICROCEPHALIC PINHEAD. MUTATION IS WHAT YOU ARE LOOKING FOR THERE, NOT NATURAL SELECTION. HERE YOU CAN SEE HIS IGNORANCE OF BIOLOGY.
An open thermodynamic system is not the answer either since simply adding energy to existing machinery will not change what is there already to a new machine.
BUT WHAT IF THE MACHINERY IN QUESTION CAN BE REFORMED, LIKE OUR DNA IS? LOOK AT MUTATIONS- THEY CAUSE CHANGES IN THE MACHINE THAT FORMS OUR PROTEINS ETC ETC. IN FACT, I SUGGEST THAT MUTATIONS MAY WELL BE THERMODYNAMICALLY FAVOURED, SINCE WE ARE DEALING WITH THE ATOMIC LEVEL, WHERE THINGS CAN CHANGE WITHOUT ANY DEFINITE INPUT.
To quote Wilder Smith whose book 'The natural sciences know nothing of evolution' is available on the web - p. 146 "Today it is simply unscientific to claim that the fantastically reduced entropy of the human brain, of the dolphin's sound lens, and of the eye of a fossilised trilobite simply "happened", for experimental experience has shown that such miracles just do not "happen"."
MORE QUOTING, NO EVIDENCE. WHAT IS THIS SIMPLY HAPPENED THING? DO THEY THINK THAT THEY DROPPED OUT OF THE SKY ONE DAY? NOT TO MENTION THE HUGE AMOUNT OF EVIDENCE SHOWING THAT THEY CAN EVOLVE ANYWAY.
My position is to side with experimental science and not with 'just so' attempts to get round the clear evidence of design in nature. At the very least these matters should be critically considered in science teaching today.
WHAT EXPERIMENTAL SCIENCE, YOU MORON? CREATIONISTS, NAY, CRETINISTS LIKE YOURSELF HAVE NOT DONE ANY. WHERE ARE THE DETAILED THERMODYNAMIC CALCULATIONS SHOWING THAT YOUR STATEMENTS ABOUT FREE NERGY LEVELS IN CELLS ETC ARE CORRECT? A MAN OF YOUR EDUCATION CAN SURELY PERFORM SUCH CALCULATIONS, AND DAZZLE US ALL WITH YOUR GRASP OF SCIENCE!
I don’t think we’ll see anything from Mcintosh about his scientific basis for his belief. Suffice to say, he is a laughing stock.
Ultimately, the most laughable thing about it is that the Creationists come across as arch materialists, with their insistence on machinery in cells.
Other entertainment can be had here:
http://idintheuk.blogspot.com/
http://www.exilefromgroggs.blogspot.com/
Meanwhile, on the BBC blog here:
http://www.bbc.co.uk/blogs/ni/
I have run into such a monumentally stupid poster that even I have trouble believing it. They insist on conflating methodological naturalism, which is what science does, considering only things which are material, that can be sensed etc, with philosophical naturalism, which says that there are only natural things in the universe, that there are no supernatural entities. So he claims that science is atheistic, because it says nothing about god, indeed can only work when you disregard supernatural entities.
Well, duh.
Science only looks at material things. It has nothing to say about gods.
So, if you are concerned about TiS and their stupidity, please write to your MP expressing your concern.
* Evolutionary science has undergone at least 2 revisions since Darwin’s time. These have integrated what we now know of genetics and other influences upon evolution into the science of Evolutionary Biology. More information here:
http://www.talkorigins.org/faqs/modern-synthesis.html
It is worth reminding people that Creationists will quote mine sentences from scientific sources that appear to damage Evolutionary theory, whilst ignoring that the source as a whole actually backs evolution. It is quote common for scientists to say something like “This blows a huge hole in the current way of thinking about this.” (They are human after all and like hyperbola just like the rest of us, not to mention puffing themselves up) The Creationists then quote this sentence, whilst ignoring that the next sentence says “Fortunately, my work shows that if you integrate this, this and that, because of X, then actually its no problem at all and it all fits nicely within Evolution”.
too much software to learn
Now I have this blog, in order to more personalise interactions within a large section of the blogosphere, I find that I shall have to learn even more software gubbins. I know they try and make it easy for us, but now I have to figure out how to ensure that the full width of pictures loads. The posts I have made below have about half the width of each photo missing, which obviously is no use.
This is on top of 2 different browsers, multiple e-mail systems, MS word, excel, not to mention the stuff I need to use to burn CD's, my antivirus software, various kinds of entertainment software, and so on.
It was so much simpler 11.5 years ago when I first met the internet and e-mail. ONe program for each, and one word processing program and that was about it.
This is on top of 2 different browsers, multiple e-mail systems, MS word, excel, not to mention the stuff I need to use to burn CD's, my antivirus software, various kinds of entertainment software, and so on.
It was so much simpler 11.5 years ago when I first met the internet and e-mail. ONe program for each, and one word processing program and that was about it.
Thursday, January 25, 2007
Melted copper and disaster
Today I managed to melt some copper and break my bellows.
On Friday night I had set up my furnace, with rather a large furnace volume. On Saturday morning I lit the charcoal, and realized that it was not going to work, since the bellows were too far from the charcoal and the overall volume was too large, the charcoal would spread out too easily. So I pushed one end in and swapped the bellows round to the other end. Doing this meant the hot zone was barely 10 inches a side. I keep forgetting how small is better in this situation. Furnace performance depends upon the fuel supply, and how much air you can get into it, so if the internal volume is very large, you cannot get enough air in to keep the charcoal burning fast enough to produce the heat needed. A bit of wind will get you above 5 or 600 degrees, but in order to get to high temps you have to get bellows blowing straight into the heart of the fire.
This is what the set up was like:
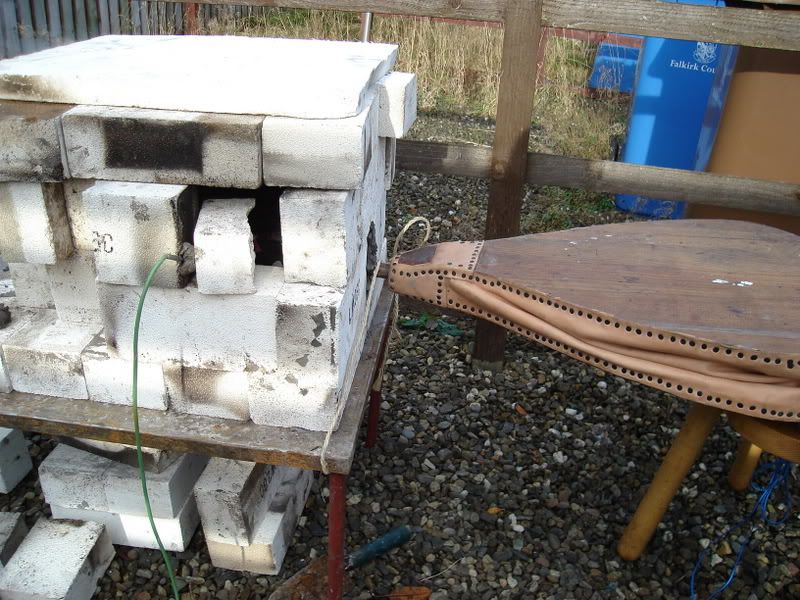
My bellows are tied onto the wooden collapsible stool I have.
This is the raw material:
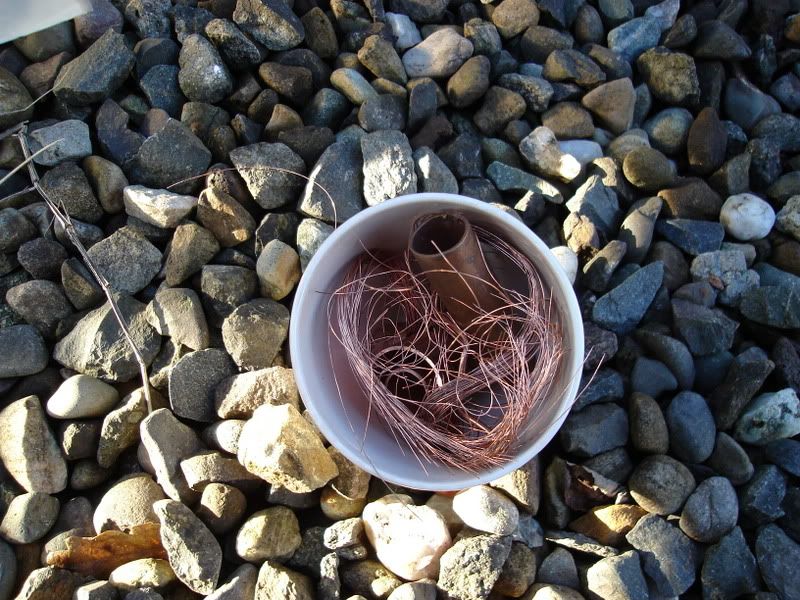
Copper wire and bits off the end of pipes, placed in a small crucible. I was hoping on getting a puddle of copper in the bottom of the crucible, which required a temperature above 1083C, the melting point of copper.
So, after some puffing with the bellows, I managed to get the temperature around 1100, and held it at that, or as high 1140 or so, for several minutes at a time, pausing only to add more charcoal. This was small bit of charcoal, maybe a cm or 2 long.
This is what it looked like at that stage:
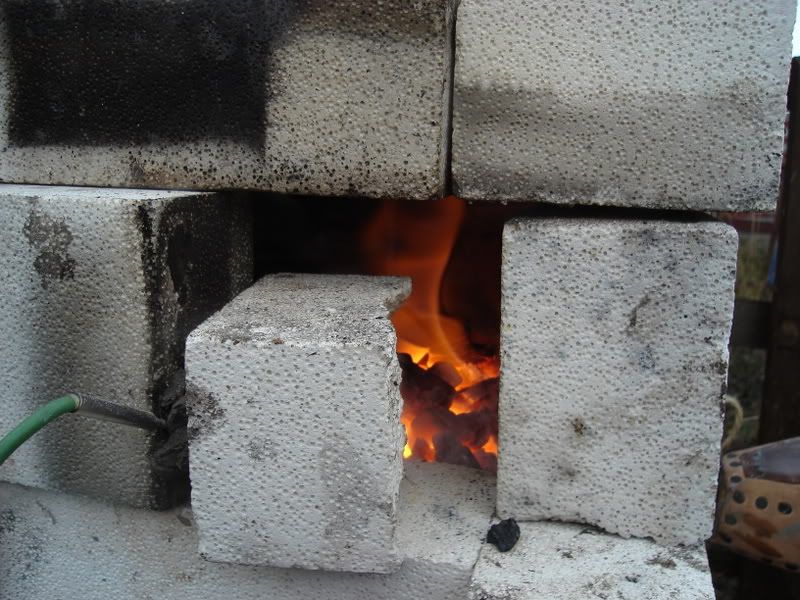
The green bit of wire to the left of the picture is the thermocouple probe- several feet of plastic coated wire attached to a stainless steel sheath encasing the thermocouple wires. The problem is, that to maintain that temperature, and a high of 1180C (Any more and the thermocouple would have been damaged) I had to work the bellows almost constantly, and also throw on small lumps of charcoal at frequent intervals. I could follow the temperature changes as the smaller bits of charcoal were consumed. At one point I was holding around 1140 with only slow puffing of the bellows, for several minutes, but then the temperature began to fall, and I think it would have been due to the higher surface area small stuff having been consumed, leaving only the larger bits that would burn away more slowly.
So this went on for half an hour or so. All I could see of the crucible with the copper in it was the top of a bit of pipe, which had clearly not melted. Which was annoying, so I kept pumping the bellows, trying to maintain a high enough temperature.
Then I smelt something burning, which was odd. I knew the copper pipe out of the bellows was getting hot, I had already dowsed it with water several times. But this was a fishy smell….
Then the bellows went a bit funny, and I knew something was wrong. It turned out that this hole:
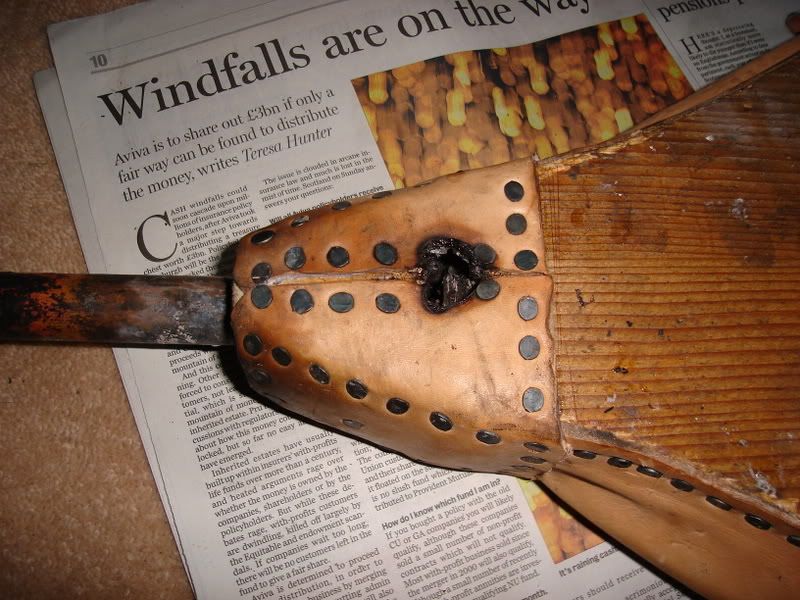
Had been burnt in them. It looked like I had managed to suck a small bit of charcoal back into the valve bit of the bellows. Now, several times during my puffing I had heard sounds like hot air was being drawn back into the bellows through the copper tube. It seems that maybe I was not drawing the bellows in the right way, although it is not clear how.
So, this is the melted copper:
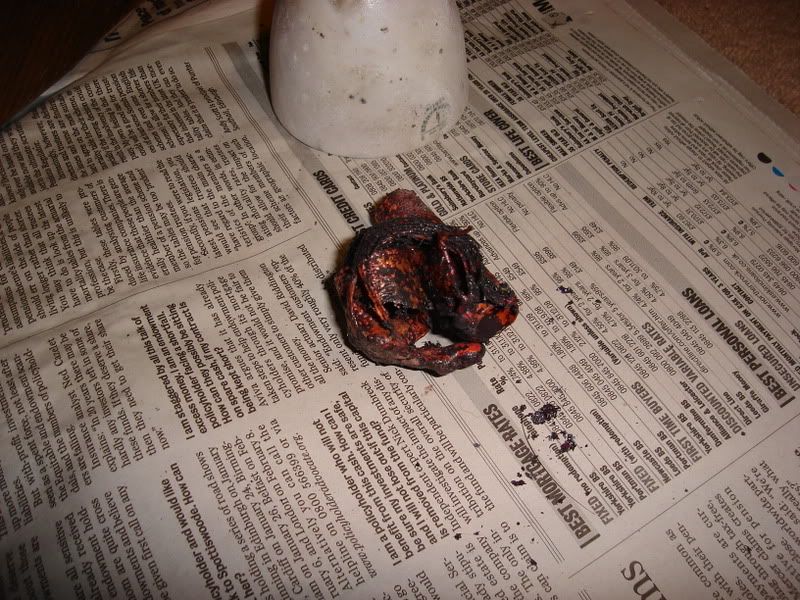
Not much, is it? The lower bits got hot enough to melt when they were touching the crucible, but the temperature never got hot enough for long enough that the upper bits melted into them. However today’s experiments show that it is possible to get high enough temperatures to melt copper, which is therefore high enough to make various copper alloys. It’s the glass making that will be tricky.
I need to get the bellows fixed and get a second pair. In the meantime I can play with pewter casting, since pewter will melt over a good charcoal or wood fire, the modern Britannia metal variety melts around 210C.
On Friday night I had set up my furnace, with rather a large furnace volume. On Saturday morning I lit the charcoal, and realized that it was not going to work, since the bellows were too far from the charcoal and the overall volume was too large, the charcoal would spread out too easily. So I pushed one end in and swapped the bellows round to the other end. Doing this meant the hot zone was barely 10 inches a side. I keep forgetting how small is better in this situation. Furnace performance depends upon the fuel supply, and how much air you can get into it, so if the internal volume is very large, you cannot get enough air in to keep the charcoal burning fast enough to produce the heat needed. A bit of wind will get you above 5 or 600 degrees, but in order to get to high temps you have to get bellows blowing straight into the heart of the fire.
This is what the set up was like:
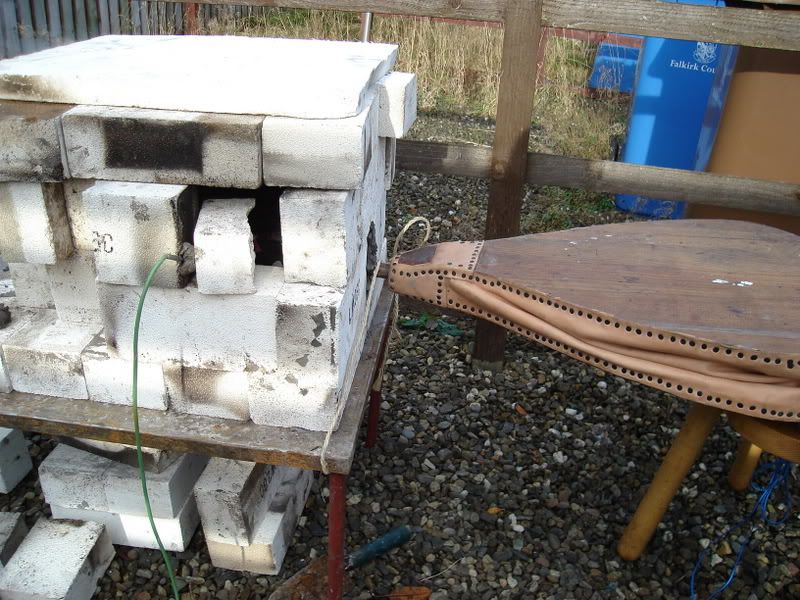
My bellows are tied onto the wooden collapsible stool I have.
This is the raw material:
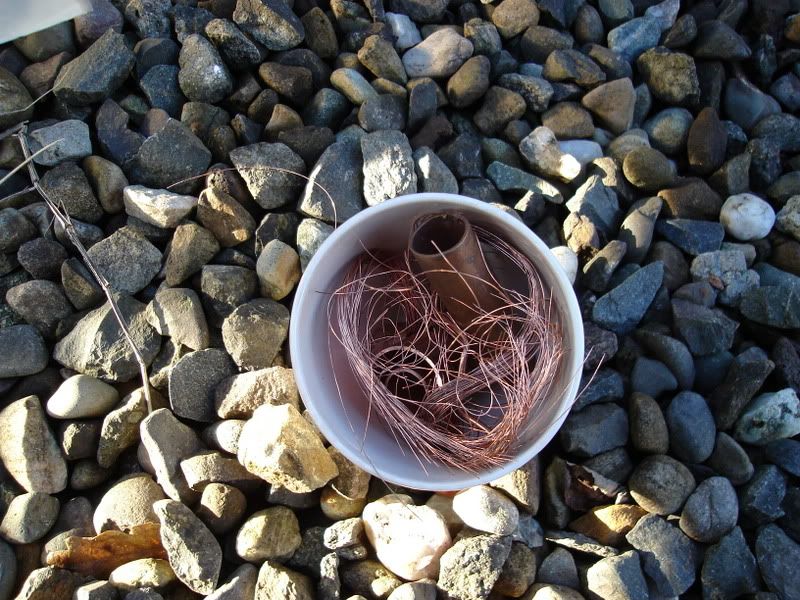
Copper wire and bits off the end of pipes, placed in a small crucible. I was hoping on getting a puddle of copper in the bottom of the crucible, which required a temperature above 1083C, the melting point of copper.
So, after some puffing with the bellows, I managed to get the temperature around 1100, and held it at that, or as high 1140 or so, for several minutes at a time, pausing only to add more charcoal. This was small bit of charcoal, maybe a cm or 2 long.
This is what it looked like at that stage:
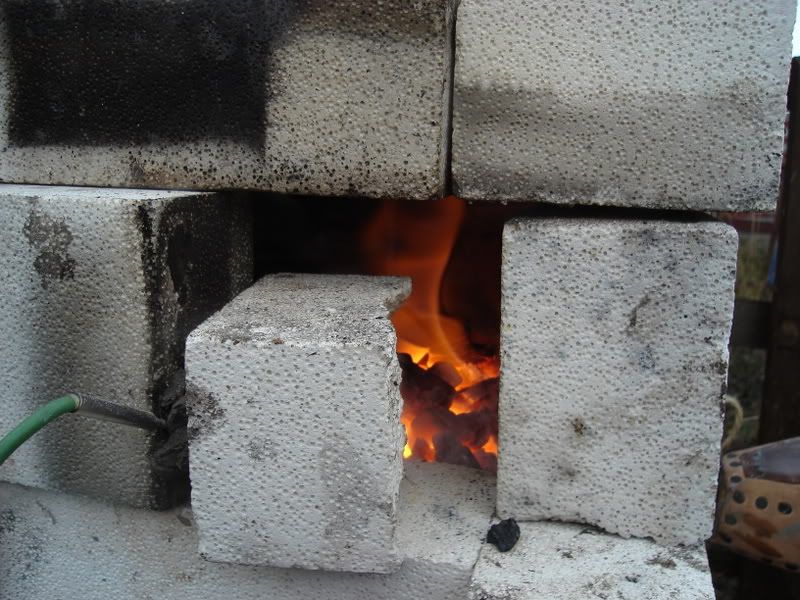
The green bit of wire to the left of the picture is the thermocouple probe- several feet of plastic coated wire attached to a stainless steel sheath encasing the thermocouple wires. The problem is, that to maintain that temperature, and a high of 1180C (Any more and the thermocouple would have been damaged) I had to work the bellows almost constantly, and also throw on small lumps of charcoal at frequent intervals. I could follow the temperature changes as the smaller bits of charcoal were consumed. At one point I was holding around 1140 with only slow puffing of the bellows, for several minutes, but then the temperature began to fall, and I think it would have been due to the higher surface area small stuff having been consumed, leaving only the larger bits that would burn away more slowly.
So this went on for half an hour or so. All I could see of the crucible with the copper in it was the top of a bit of pipe, which had clearly not melted. Which was annoying, so I kept pumping the bellows, trying to maintain a high enough temperature.
Then I smelt something burning, which was odd. I knew the copper pipe out of the bellows was getting hot, I had already dowsed it with water several times. But this was a fishy smell….
Then the bellows went a bit funny, and I knew something was wrong. It turned out that this hole:
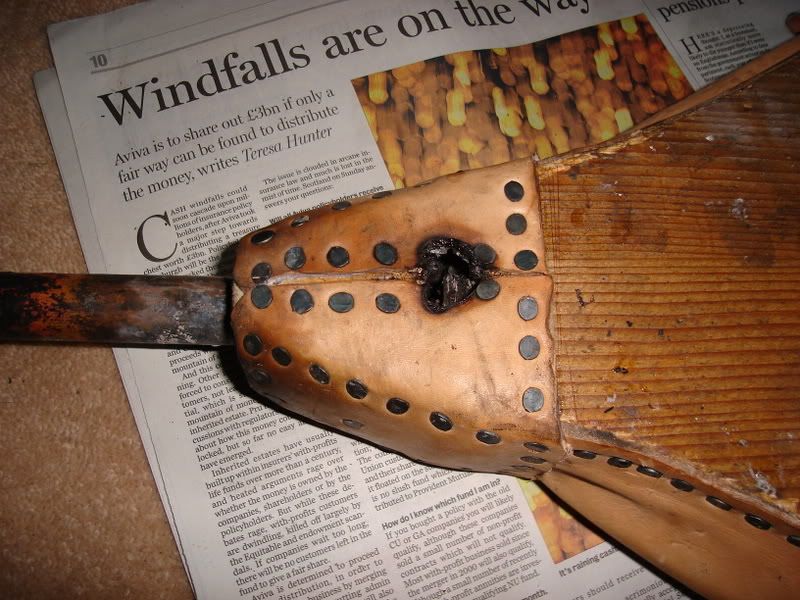
Had been burnt in them. It looked like I had managed to suck a small bit of charcoal back into the valve bit of the bellows. Now, several times during my puffing I had heard sounds like hot air was being drawn back into the bellows through the copper tube. It seems that maybe I was not drawing the bellows in the right way, although it is not clear how.
So, this is the melted copper:
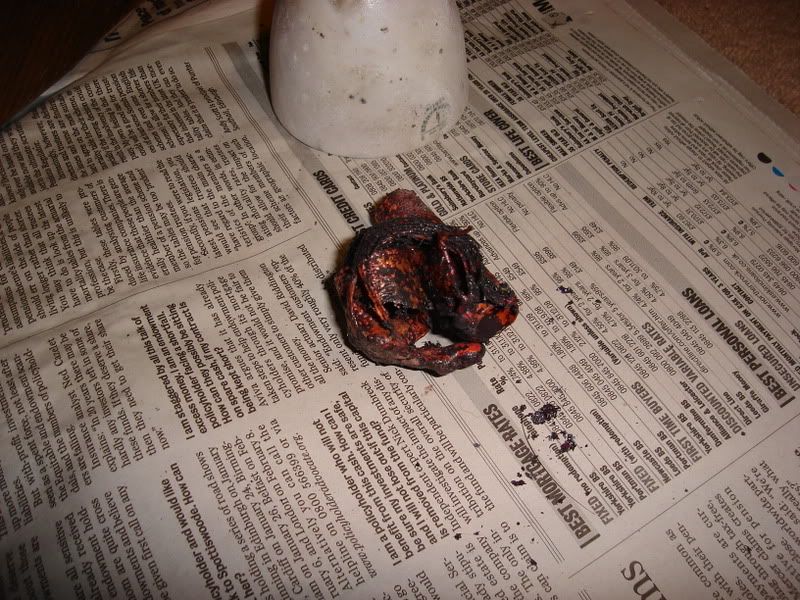
Not much, is it? The lower bits got hot enough to melt when they were touching the crucible, but the temperature never got hot enough for long enough that the upper bits melted into them. However today’s experiments show that it is possible to get high enough temperatures to melt copper, which is therefore high enough to make various copper alloys. It’s the glass making that will be tricky.
I need to get the bellows fixed and get a second pair. In the meantime I can play with pewter casting, since pewter will melt over a good charcoal or wood fire, the modern Britannia metal variety melts around 210C.
Burning things!
Today I burnt stuff. I have never really gotten rid of some interest in burning things, I was sticking bits of wood in the fire as a child, but rest assured, I do not engage in wanton destruction. (Although it would be so easy. I’m sometimes amazed at how uncommon it is for people to actually destroy things, but that’s another post)
The aim today was twofold- to burn beech wood and bracken, in order to get two kinds of ashes for the production of sal alkali, or in other words alkaline salts, usually of potassium. Beech wood is recommended by Biringuccio and others, and bracken is known to contain large amounts of potassium salts, and is recommended in other books.
Raw materials, bracken and wood:
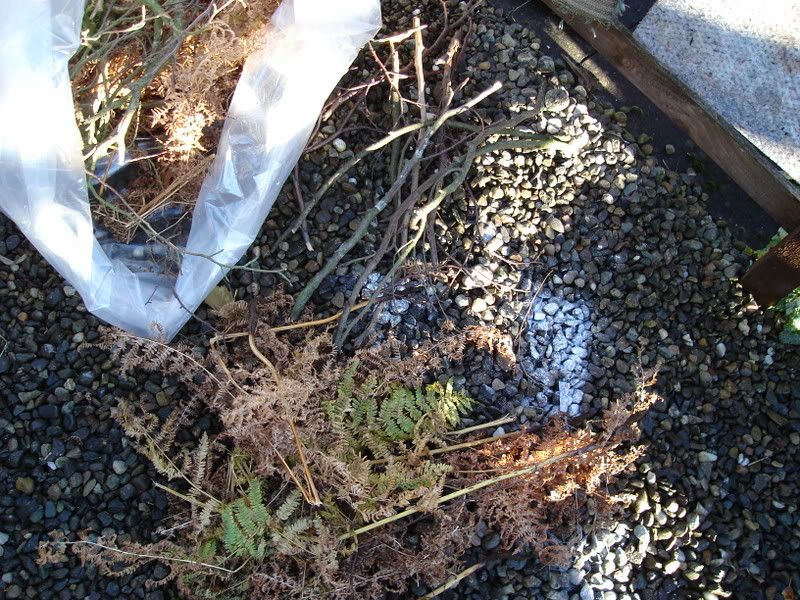
So, the first thing I did was build my furnace. I shall explain it and its genesis in a later post. Here is the inside of it:
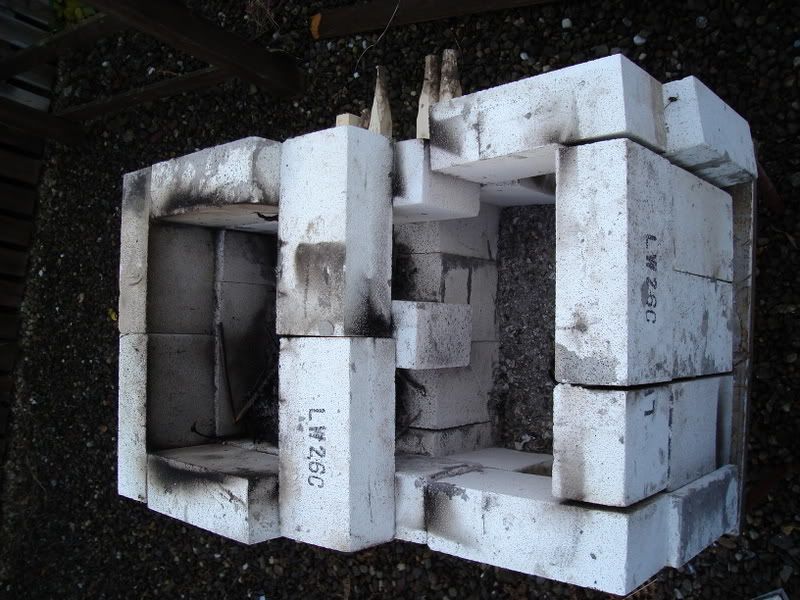
On the right hand side is the lower section, on the left the higher section. I forgot to re-orientate the photo before posting it, so it is on its side rather than being vertical. It should be clear that there is a gap between some firebricks between the lower and upper sections. The lower section is open at the sides, and contained the beech wood. The upper section was open at the bottom and the top. This is essentially an attempt at a reverberatory furnace, where the heat and combustible material from the lower chamber rises up into the upper chamber, and heats whatever is in there.
This can sort of be seen here:
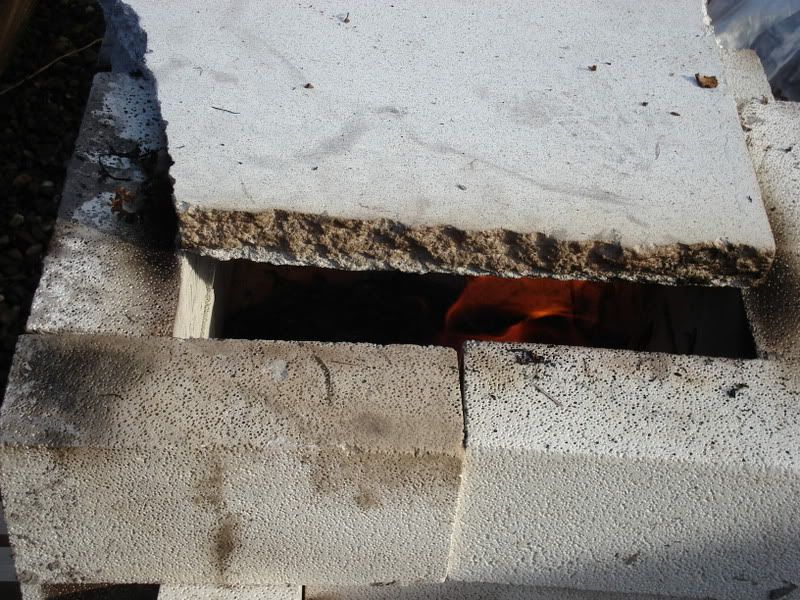
Here you can see flames from the wood rising up through the upper chamber. You have to use wood for this, as far as I understand it, so that you get lots of nice volatiles distilling off and burning as they rise.
The basic work was easy, the thing that took a long time was putting the furnace together, and covering gaps with clay, that took nearly an hour. Actually burning all the wood took only 45 minutes. I simply stuffed the upper compartment with bracken, and the lower one with fine twigs and newspaper, and lit the newspaper. After that the natural chimney effect took over, and the fire got going ok, although a little slowly. I just had to feed more bracken in the top as the previous stuff burnt.
I checked the temp half way through using my thermocouple. The temp in the wood fire was 680 to over 700 when the wind blew, but only a bit over 300 in the bracken compartment.
Results and discussion
The end results were a small amount of beech ash, and a small amount of bracken ash, with some unburnt stems. The problem was that I had not dried the bracken properly, and so the root stems, which were thick and wet did not catch light very easily. The wood used was a smidgen damp, which did not help, but burnt well enough, the problem was the lack of draft. Doing it in my tiny drying area, in the shade of a fence, on a not very windy day, was not helpful. I had to use the bellows to really get it going. The problem is that a reverbertory furnace works by wind, and if there is no wind, it wont work well. Also the wood used should be totally dry, and not too thick, I think that anything more than a cm in diameter is not much use, since it will not burn fast enough. Remember, burnt wood is an insulator, that is why they use it on fire doors. I also didn’t have enough wood at all, I could easily have kept feeding it for ages, with enough wood available.
But now I have some ashes to play with. See my next post for what I shall do with them.
The aim today was twofold- to burn beech wood and bracken, in order to get two kinds of ashes for the production of sal alkali, or in other words alkaline salts, usually of potassium. Beech wood is recommended by Biringuccio and others, and bracken is known to contain large amounts of potassium salts, and is recommended in other books.
Raw materials, bracken and wood:
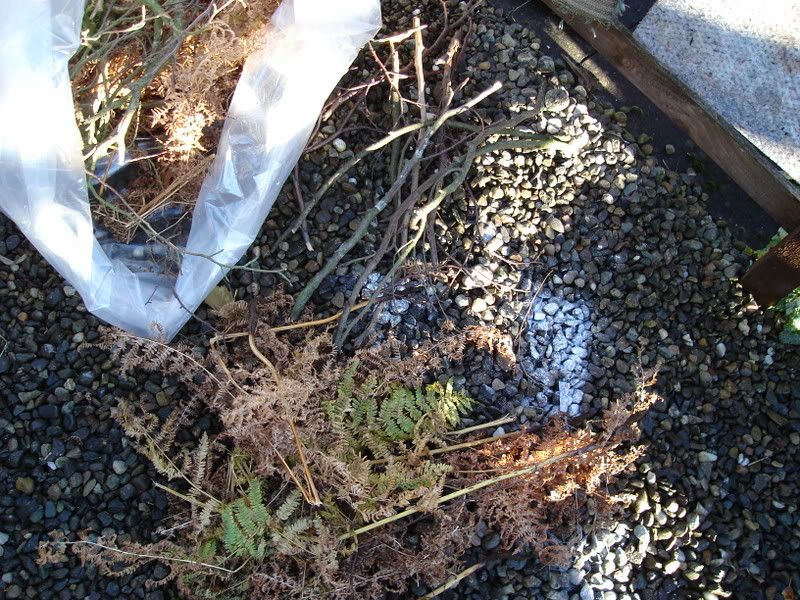
So, the first thing I did was build my furnace. I shall explain it and its genesis in a later post. Here is the inside of it:
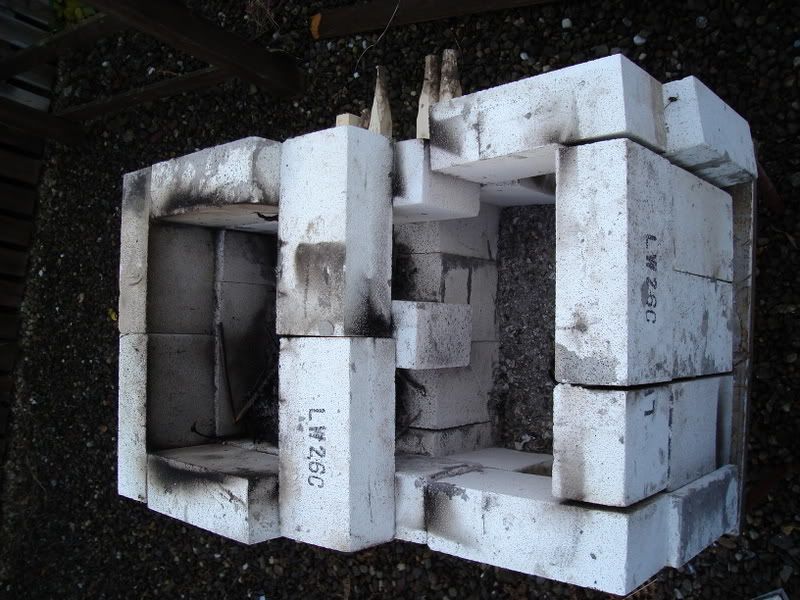
On the right hand side is the lower section, on the left the higher section. I forgot to re-orientate the photo before posting it, so it is on its side rather than being vertical. It should be clear that there is a gap between some firebricks between the lower and upper sections. The lower section is open at the sides, and contained the beech wood. The upper section was open at the bottom and the top. This is essentially an attempt at a reverberatory furnace, where the heat and combustible material from the lower chamber rises up into the upper chamber, and heats whatever is in there.
This can sort of be seen here:
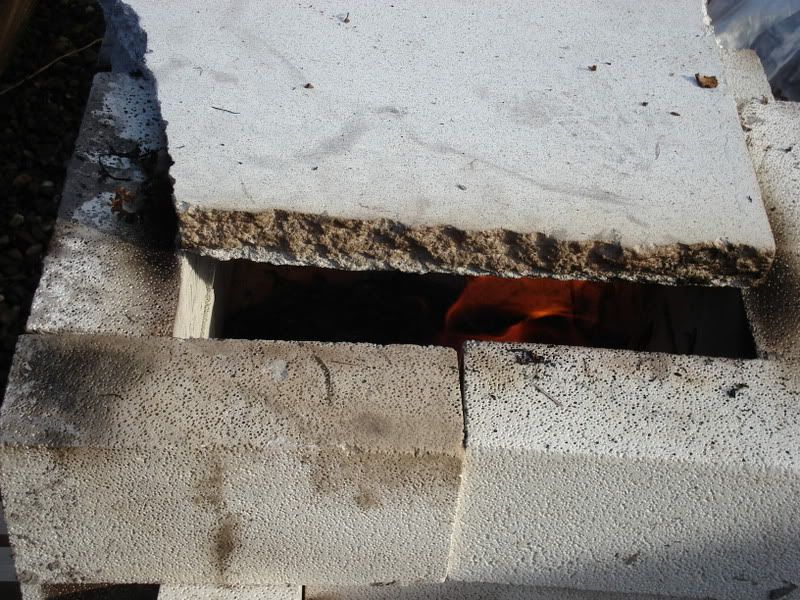
Here you can see flames from the wood rising up through the upper chamber. You have to use wood for this, as far as I understand it, so that you get lots of nice volatiles distilling off and burning as they rise.
The basic work was easy, the thing that took a long time was putting the furnace together, and covering gaps with clay, that took nearly an hour. Actually burning all the wood took only 45 minutes. I simply stuffed the upper compartment with bracken, and the lower one with fine twigs and newspaper, and lit the newspaper. After that the natural chimney effect took over, and the fire got going ok, although a little slowly. I just had to feed more bracken in the top as the previous stuff burnt.
I checked the temp half way through using my thermocouple. The temp in the wood fire was 680 to over 700 when the wind blew, but only a bit over 300 in the bracken compartment.
Results and discussion
The end results were a small amount of beech ash, and a small amount of bracken ash, with some unburnt stems. The problem was that I had not dried the bracken properly, and so the root stems, which were thick and wet did not catch light very easily. The wood used was a smidgen damp, which did not help, but burnt well enough, the problem was the lack of draft. Doing it in my tiny drying area, in the shade of a fence, on a not very windy day, was not helpful. I had to use the bellows to really get it going. The problem is that a reverbertory furnace works by wind, and if there is no wind, it wont work well. Also the wood used should be totally dry, and not too thick, I think that anything more than a cm in diameter is not much use, since it will not burn fast enough. Remember, burnt wood is an insulator, that is why they use it on fire doors. I also didn’t have enough wood at all, I could easily have kept feeding it for ages, with enough wood available.
But now I have some ashes to play with. See my next post for what I shall do with them.
Wednesday, January 24, 2007
First Post
This is my new blog. I already have a Livejournal, but am interested in a bit wider coverage for what I am doing, and also because it gives me more presence in the blogs I post on.
I shall be covering my experiments on alchemy and medieval chemistry and technology, as well as the occaisional rant on politics or creationism or some other stupidity.
Are you bored yet?
Come back in a few days when I have some old posts up, they are more interesting.
I shall be covering my experiments on alchemy and medieval chemistry and technology, as well as the occaisional rant on politics or creationism or some other stupidity.
Are you bored yet?
Come back in a few days when I have some old posts up, they are more interesting.
Subscribe to:
Posts (Atom)